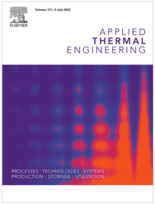
Modèle thermodynamique d'un moteur Stirling non idéal adapté à l'intégration dans les systèmes énergétiques globaux.
Non-ideal Stirling engine thermodynamic model suitable for the integration into overall energy systems.
Auteurs : ARAOZ J. A., SALOMON M., ALEJO L., et al.
Type d'article : Article
Résumé
The reliability of modelling and simulation of energy systems strongly depends on the prediction accuracy of each system component. This is the case of Stirling engine-based systems, where an accurate modelling of the engine performance is very important to understand the overall system behaviour. In this sense, many Stirling engine analyses with different approaches have been already developed. However, there is a lack of Stirling engine models suitable for the integration into overall system simulations. In this context, this paper aims to develop a rigorous Stirling engine model that could be easily integrated into combined heat and power schemes for the overall techno-economic analysis of these systems. The model developed considers a Stirling engine with adiabatic working spaces, isothermal heat exchangers, dead volumes, and imperfect regeneration. Additionally, it considers mechanical pumping losses due to friction, limited heat transfer and thermal losses on the heat exchangers. The model is suitable for different engine configurations (alpha beta and gamma engines). It was developed using Aspen Custom Modeller® (ACM®) as modelling software. The set of equations were solved using ACM® equation solver for steady-state operation. However, due to the dynamic behaviour of the cycle, a C++ code was integrated to solve iteratively a set of differential equations. This resulted in a cyclic steady-state model that calculates the power output and thermal requirements of the system. The predicted efficiency and power output were compared with the numerical model and the experimental work reported by the NASA Lewis Research Centre for the GPU-3 Stirling engine. This showed average absolute errors around ±4% for the brake power, and ±5% for the brake efficiency at different frequencies. However, the model also showed large errors (±15%) for these calculations at higher frequencies and low pressures. Additional results include the calculation of the cyclic expansion and compression work; the pressure drop and heat flow through the heat exchangers; the conductive, shuttle effect and regenerator thermal losses; the temperature and mass flow distribution along the system; and the power output and efficiency of the engine. These results show that the model allows an extensive study of different parameters of the engine and thus it is suitable for design optimization studies. In addition, it also presents the capability for the integration into overall Stirling engine combined heat and power systems and therefore will allow the performance evaluation of the engine integrated on these systems.
Détails
- Titre original : Non-ideal Stirling engine thermodynamic model suitable for the integration into overall energy systems.
- Identifiant de la fiche : 30014518
- Langues : Anglais
- Sujet : Technologie
- Source : Applied Thermal Engineering - vol. 73 - n. 1
- Date d'édition : 12/2014
- DOI : http://dx.doi.org/10.1016/j.applthermaleng.2014.07.050
Liens
Voir d'autres articles du même numéro (44)
Voir la source
Indexation
- Thèmes : Domaines connexes au froid
- Mots-clés : Thermodynamique; Technologie; Énergie; Stirling; Simulation; Moteur; Cogénération
-
A three-dimensional CFD simulation study to red...
- Auteurs : PEREZ J. A., OROSA J.A., GRUEIRO T.
- Date : 05/02/2016
- Langues : Anglais
- Source : Applied Thermal Engineering - vol. 94
Voir la fiche
-
Integrating Li-Fi wireless communication and en...
- Auteurs : HUANG Q., LI X., SHAURETTE M.
- Date : 14/07/2014
- Langues : Anglais
- Source : 2014 Purdue Conferences. 3rd International High Performance Buildings Conference at Purdue.
- Formats : PDF
Voir la fiche
-
Opportunities and challenges for a sustainable ...
- Auteurs : CHU S., MAJUMDAR A.
- Date : 16/08/2012
- Langues : Anglais
- Source : Nature - vol. 488 - n. 7411
Voir la fiche
-
Depuis le filaire jusqu'à la lumière...
- Auteurs : POGGI P.
- Date : 12/2015
- Langues : Français
- Source : La revue pratique du froid et du conditionnement d'air - n. 1041
Voir la fiche
-
Propuesta de cocina solar fotovoltaica análisis...
- Auteurs : LECUONA-NEUMANN A., SÁNCHEZ-BODAS M. A., VENTAS-GARZÓN R.
- Date : 03/05/2016
- Langues : Espagnol
- Source : CYTEF 2016. VIII Congreso Ibérico y VI Congreso Iberoamericano de las Ciencias y Técnicas del Frío, Coimbra-Portugal, 3-6 mayo, 2016.
- Formats : PDF
Voir la fiche