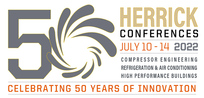
Modélisation d’un compresseur à bobine à l’aide d’un fluide couplé et d’un solveur solide avec une méthodologie CFD avec cellule découpée et affinement adaptatif du maillage.
Modeling a spool compressor using a coupled fluid and solid solver with cut-cell based CFD methodology with adaptive mesh refinement.
Numéro : 1140
Auteurs : WAIKAR A., ROWINSKI D., KEMP G., OROSZ J., BRADSHAW C.
Résumé
The novel spool compressor provides a new rotating compression mechanism with applications in residential and commercial air conditioning systems. The spool compressor features a rotor and a constrained sliding vane which create a positive-displacement compression process. An array of poppet valves allows for the discharge of the compressed fluid. The combination of the suction process, the compression process, and the discharge process exhibit a strong degree of interdependence on the fluid flow and the motion of the components. It is essential to understand this complex fluid flow and its interaction with the moving components inside the compressor to improve its design and efficiency. Computational Fluid Dynamics (CFD) has been increasingly used for the design and analysis of compressors. The spool compressor’s interconnected components undergo both translation and rotation, and the valve motion is dependent on the flow field. These factors make the process of defining the computational grid on which the governing equations are solved highly non-trivial. Furthermore, in these models, it is imperative to ensure the grid discretization yields a sufficiently small numerical error relative to the experimental, modeling, and gross error.
This paper deals with the development and application of a CFD model for a spool compressor. An automatic meshing approach is used to tackle the challenge of moving geometries. Furthermore, adaptive mesh refinement is used to dynamically change the mesh based on local velocity and temperature at each time step. Thus, the Cartesian cut-cell based meshing requires no user meshing, with the mesh concentrated in the regions of large gradients. An explicit coupled approach is used to account for the fluid-structure interaction between valves and the flow field. The displacement of each of the valves is constrained in one dimension along the valve post. The fluid is solved using a finite volume approach, whereas equations of rigid body motion are used to solve for the valve motion of an arbitrary number of discharge valves. The working fluid used for the simulation is R134a. Experimental data for mass flow rate, torque, and pressure traces at various locations is used to validate the CFD model. The results from the simulation show good agreement for the global quantities of mass flow rate and power for nearly all mesh sizes, while the instantaneous pressure traces show more sensitivity to the grid size. An appropriately fine interior mesh can resolve the internal pressure fluctuations. Furthermore, the three-dimensional flow field provides insight into valve lifts and flow across the vane tip, as well as the process efficiency.
Documents disponibles
Format PDF
Pages : 10 p.
Disponible
Gratuit
Détails
- Titre original : Modeling a spool compressor using a coupled fluid and solid solver with cut-cell based CFD methodology with adaptive mesh refinement.
- Identifiant de la fiche : 30030268
- Langues : Anglais
- Sujet : Technologie
- Source : 2022 Purdue Conferences. 26th International Compressor Engineering Conference at Purdue.
- Date d'édition : 15/07/2022
Liens
Voir d'autres communications du même compte rendu (83)
Voir le compte rendu de la conférence
Indexation
-
Thèmes :
Compresseurs;
Conditionnement d'air pour le confort - Mots-clés : CFD; Modèle; Géometrie; R134a; Simulation; Compresseur rotatif; Modélisation
-
High pressure rotary compressor CFD analysis: p...
- Auteurs : ADHIKARY P., SAHA S., PRAKASH D., et al.
- Date : 27/07/2018
- Langues : Anglais
- Source : Proceedings of the International Conference on Emerging Technologies for Sustainable and Intelligent HVAC&R Systems, Kolkata, July 27-28 2018.
- Formats : PDF
Voir la fiche
-
Modeling a scroll compressor using a Cartesian ...
- Auteurs : ROWINSKI D., PHAM H., BRANDT T.
- Date : 09/07/2018
- Langues : Anglais
- Source : 2018 Purdue Conferences. 24th International Compressor Engineering Conference at Purdue.
- Formats : PDF
Voir la fiche
-
Rotary compressor performance analysis by CFD: ...
- Auteurs : ADHIKARY P., AMAN M. B., SINGH A., et al.
- Date : 27/07/2018
- Langues : Anglais
- Source : Proceedings of the International Conference on Emerging Technologies for Sustainable and Intelligent HVAC&R Systems, Kolkata, July 27-28 2018.
- Formats : PDF
Voir la fiche
-
In-situ characterization of the size distributi...
- Auteurs : WU P., CHEN J., SOJKA P. E., LI Y., CAO H.
- Date : 10/2023
- Langues : Anglais
- Source : International Journal of Refrigeration - Revue Internationale du Froid - vol. 154
- Formats : PDF
Voir la fiche
-
A comparison of interpolation methods in fast f...
- Auteurs : LEONARD E., QIAO H., NABI S.
- Date : 24/05/2021
- Langues : Anglais
- Source : 2021 Purdue Conferences. 6th International High Performance Buildings Conference at Purdue.
- Formats : PDF
Voir la fiche