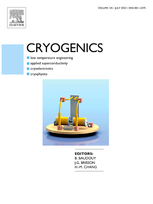
Modélisation structurelle de rubans et câbles supraconducteurs à haute température.
Structural modeling of HTS tapes and cables.
Auteurs : ALLEN N. C., CHIESA L., TAKAYASU M.
Type d'article : Article
Résumé
Structural finite element analysis (FEA) has been used as an insightful tool to investigate the electromechanical behavior of HTS REBCO tapes and twisted stacked-tape cables under tension, torsion, bending and combined loads. A novel technique was developed for modeling the layered composite structure of the 2G tapes with structural solid-shell elements in ANSYS. The FEA models produced detailed strain information for the REBCO superconducting layer which was then paired with an analytical model to predict the critical current performance of the 2G HTS tapes under various loads. Two commercially available HTS tapes (SuperPower and SuNAM) under tension, torsion and combined tension–torsion were first analyzed with FEA and compared with available experimental results at 77 K. A sharp critical current degradation was experienced at the yield strength of the tapes under tension and below a 100 mm twist-pitch under torsion. Combined tension–torsion loads had a more gradual degradation of critical current for twist-pitches of 115 mm or shorter but had a negligible difference compared to pure tension for longer twist-pitches. Using the structural solid-shell technique for modeling 2G tapes in ANSYS, an FEA methodology for simulating full scale three-dimensional HTS stacked-tape cables under pure bending was created. A model of a Twisted-Stacked Tape Cable (TSTC), a configuration first proposed at MIT, was initially developed and then adapted to the slotted-core HTS Cable-In-Conduit Conductor produced by the ENEA laboratory in Italy. The numerical axial strain of the HTS REBCO tapes within the cables as calculated by FEA were found to agree with an analytical model for two cases: perfect-slip (frictionless) and no-slip (bonded). The ENEA CICC model was also compared with recent experimental critical current data at 77 K and was found to match best using a low friction coefficient of 0.02 indicating that the tapes within the cable freely slide with respect to each other helping to reduce the axial strain during bending.
Détails
- Titre original : Structural modeling of HTS tapes and cables.
- Identifiant de la fiche : 30021234
- Langues : Anglais
- Source : Cryogenics - vol. 80
- Date d'édition : 02/2016
- DOI : http://dx.doi.org/10.1016/j.cryogenics.2016.02.002
Liens
Voir d'autres articles du même numéro (31)
Voir la source
Indexation
- Thèmes : Supraconduction
- Mots-clés : Câble supraconducteur; Ruban supraconducteur; Modélisation; Haute température
-
Reduction of alternating magnetic field losses ...
- Auteurs : KWASNITZA K., CLERC S., FLUKIGER R., et al.
- Date : 1999
- Langues : Anglais
- Source : Cryogenics - vol. 39 - n. 10
Voir la fiche
-
Modelling of 3D temperature profiles and pressu...
- Auteurs : SHABAGIN E., HEIDT C., STRAUß S., et al.
- Date : 11/2016
- Langues : Anglais
- Source : Cryogenics - vol. 81
Voir la fiche
-
AC losses in HTSC bulk and tapes: a review.
- Auteurs : CHATTOPADHYAY M. K.
- Date : 06/2000
- Langues : Anglais
- Source : J. Supercond. - vol. 13 - n. 3
Voir la fiche
-
Design of superconducting power cables.
- Auteurs : WESCHE R., ANGHEL A., JAKOB B., et al.
- Date : 1999
- Langues : Anglais
- Source : Cryogenics - vol. 39 - n. 9
Voir la fiche
-
Analysis of the influence structural defects on...
- Auteurs : SOSNOWSKI J.
- Date : 08/05/2019
- Langues : Anglais
- Source : Cryogenics 2019. Proceedings of the 15th IIR International Conference: Prague, Czech Republic, April 8-11, 2019.
- Formats : PDF
Voir la fiche