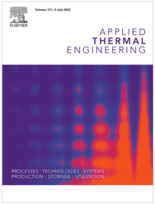
Résumé
This study presents a new interior permanent magnet (IPM) motor using rotor cooling to enhance motor power per specific weight. Unlike conventional motors that utilize air cooling through air circulation or jacket cooling through coolant circulation around the motor housing, an IPM motor that employs a forced cooling method by providing channels for housing cooling and a hollow shaft for rotor cooling is introduced in this study. The coolant circulates in the entire motor from the housing to the rotor through the proposed coolant paths. The paths include the upper housing, housing jacket, lower housing, and hollow shaft. Given that this type of cooling system forces coolant to circulate inside an IPM motor, it can provide a superior cooling effect compared with conventional cooling methods. The proposed cooling system can increase motor power because high motor speed can be achieved with a superior cooling effect by the IPM motor compared with a conventional cooling motor. A special coolant entrance path is also designed for easy coolant access, and double oil sealing is provided to prevent oil leakage. Two coolant path design parameters of serpentine type for housing and coolant hole location for the rotor are selected for optimization. After selecting the best cooling parameters, a prototype IPM motor is built with optimized parameters and tested with a motor dynamo. Temperatures at different locations are measured to validate the proposed IPM motor efficiency. After an 80-min operation, the proposed IPM motor showed a 50% decrease in temperature at the coil relative to the air-cooled motor and a 38% decrease relative to the jacket-cooled motor. However, the temperatures in the outer stator of the air-cooled and jacket-cooled motors decreased by 42% and 10%, respectively. Given that such a decrease in temperature increases the current density of the rotor and stator, more power can be obtained from a same-sized IPM motor.
Détails
- Titre original : Development of an interior permanent magnet motor through rotor cooling for electric vehicles.
- Identifiant de la fiche : 30016849
- Langues : Anglais
- Source : Applied Thermal Engineering - vol. 95
- Date d'édition : 25/02/2016
- DOI : http://dx.doi.org/10.1016/j.applthermaleng.2015.11.022
Liens
Voir d'autres articles du même numéro (37)
Voir la source
Indexation
- Thèmes : Autres applications industrielles
- Mots-clés : Aimant; Rotor; Refroidissement; Puissance; Optimisation; Moteur électrique
-
Advances in Thermal Management Technologies of ...
- Auteurs : WANG Q., WU Y., NIU S., ZHAO X.
- Date : 05/2022
- Langues : Anglais
- Source : Energies - vol. 15 - n. 9
- Formats : PDF
Voir la fiche
-
Transient cooling effect analyses for a permane...
- Auteurs : WANG S., LI Y., LI Y. Z., et al.
- Date : 25/10/2016
- Langues : Anglais
- Source : Applied Thermal Engineering - vol. 109, part A
Voir la fiche
-
A review of powertrain electrification for gree...
- Auteurs : ROBOAM X.
- Date : 10/2023
- Langues : Anglais
- Source : Energies - vol. 16 - n. 19
- Formats : PDF
Voir la fiche
-
Design and development of HTS synchronous motor...
- Auteurs : MATSUZAKI H., KIMURA Y., MIKI M., et al.
- Date : 17/07/2006
- Langues : Anglais
- Source : Multiconference CryoPrague 2006 (9th Cryogenics 2006, ICEC 21, ICMC'06)
- Formats : PDF
Voir la fiche
-
La supraconductivité et l'électrotechnique.
- Auteurs : LAUMOND Y.
- Date : 11/1995
- Langues : Français
- Source : Rev. gén. Froid - vol. 85 - n. 958
Voir la fiche