La fabrication additive de régénérateurs pour le froid calorique
Dans de nombreux domaines de l’ingénierie, la fabrication additive permet d’obtenir des produits complexes et multifonctionnels qui ne pourraient pas être fabriqués à l’aide de méthodes traditionnelles. Dans le domaine du froid calorique, la fabrication additive permet d’optimiser la géométrie des régénérateurs, et donc d’améliorer les performances des technologies de froid magnétocalorique et élastocalorique en particulier. Ce document de synthèse présente les bases des procédés de fabrication additive, les différents types de froid calorique, et les avancées de la recherche sur la fabrication additive de régénérateurs caloriques.
Qu’est-ce que la fabrication additive ?
Le terme « fabrication additive » englobe plusieurs technologies différentes qui permettent de fabriquer des produits de manière additive. Cela signifie qu’au lieu de soustraire de la matière d’une pièce en vrac, comme cela se fait dans les processus de fabrication conventionnels, tels que la découpe et le fraisage, le matériau est ajouté couche par couche pour former le produit souhaité. Il est à noter que la fabrication additive est plus communément appelée impression 3D.
Sept types de procédés de fabrication additive
Il existe plusieurs types distincts de procédés de fabrication additive basées sur certaines caractéristiques clés [1].
- Jet de matière. Ici, un matériau est déposé sur un substrat sous forme de gouttelettes pour former des couches de matériau imprimé. Cette méthode de fabrication additive est particulièrement privilégiée pour la fabrication de couches minces [2, 3].
- Stéréolithographie. Dans ce processus, un plastique liquide est solidifié par le passage d’un faisceau laser émetteur de lumière UV pour obtenir une géométrie 3D très détaillée. Cette méthode ne peut pas être utilisée pour le traitement des métaux.
- Projection de liant. Un agent liant liquide est utilisé pour lier des particules de matériau afin de former la pièce souhaitée. Le procédé par projection de liant est plutôt rapide et n’implique aucun processus à haute température. Néanmoins, si des pièces métalliques ayant des propriétés mécaniques relativement bonnes doivent être produites, un traitement thermique est ensuite nécessaire pour fritter les particules métalliques et brûler l’agent liant.
- Extrusion de matériau. Ici, le matériau est extrudé couche par couche à partir d’une buse chauffée pour former un objet final. C’est probablement le procédé de fabrication additive le plus populaire, car les imprimantes d’extrusion de matériaux sont plutôt bon marché. Les filaments plastiques sont les matériaux les plus couramment utilisés dans cette technique. Toutefois, des matériaux composites sont également disponibles, tels que la sciure de bois ou les déchets de coquille de cacao liés à un plastique biodégradable [4, 5], la poudre métallique liée à un polymère approprié [6], etc.
- Fusion sur lit de poudre. Ici, la poudre de matériau, de métal ou de polymère est répartie sur une plate-forme construite en couche mince à l’aide d’un revêtement. Ensuite, le matériau est fondu ou fritté sélectivement par un laser ou un faisceau d’électrons. Une autre couche mince du matériau est ensuite appliquée et le processus est répété jusqu’à ce que la pièce souhaitée soit produite. La qualité de surface et les propriétés mécaniques des pièces produites dépendent fortement de la densité d’énergie appliquée, de la vitesse de balayage, de la stratégie d’éclosion et, bien sûr, de la taille et de la morphologie de la poudre [7]. Parmi les matériaux les plus couramment utilisés pour ce procédé figurent le nylon, l’aluminium, l’acier, le titane et le cuivre.
- Stratification de couches. Ici, des feuilles ou plaques de matériau sont liées ensemble soit par soudage par ultrasons, soit par l’application d’un adhésif. Ce procédé permet de lier différents matériaux entre eux. La forme finale des feuilles laminées est découpée au couteau ou au laser.
- Dépôt de matière sous énergie concentrée. Il s’agit d’un procédé de fabrication additive très complexe dans lequel plusieurs bras se déplacent autour d’un objet fixe et déposent un matériau qui est ensuite fondu par un laser ou un faisceau d’électrons. Les matériaux les plus populaires pour ce procédé sont les fils ou les poudres métalliques.
Naturellement, certaines techniques de fabrication additive sont plus adaptées à des applications spécifiques que d’autres. Par conséquent, l’accent sera mis dans ce document sur les techniques qui ont déjà été appliquées pour fabriquer des régénérateurs pour des applications de froid calorique.
Qu’est-ce que le froid calorique ?
Le froid calorique est une alternative écologique à la technologie de compression de vapeur. Dans le froid calorique, des régénérateurs poreux ou perméables à l’état solide sont utilisés pour générer un effet de chauffage ou de refroidissement. Il existe quatre types de froid calorique : magnétocalorique, élastocalorique, électrocalorique, barocalorique.
Le principe du froid calorique, comparé avec la technologie de compression de vapeur, est présenté dans la figure 1 et résumé dans le tableau 1. Le terme « changement de champ » est utilisé pour désigner aussi bien le changement des champs magnétiques, qu’électriques et mécaniques.
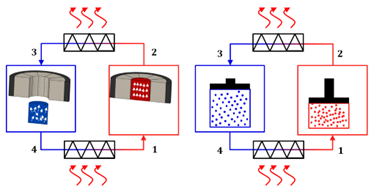
Tableau 1. Comparaison des processus de froid calorique et de compression de vapeur au cours d’un cycle frigorifique.
N° de processus | Froid calorique | Compression de vapeur |
---|---|---|
1 - 2 | Changement de champ adiabatique | Compression isentropique |
2 - 3 | Rejet de chaleur à champ constant vers le puits de chaleur | Rejet de chaleur à pression constante dans le condenseur |
3 - 4 | Changement de champ adiabatique | Étranglement dans un détendeur |
4 - 1 | Absorption de la chaleur de la source de chaleur en champ constant | Absorption de chaleur à pression constante dans l'évaporateur |
Froid magnétocalorique
Ici, les matériaux magnétocaloriques, tels que le gadolinium et ses alliages ou la famille d’alliages à base de LaFeSi, sont exposés à une modification périodique du champ magnétique externe. Cela provoque des changements dans le réseau du matériau, ce qui entraîne la génération de chaleur lorsque le matériau est magnétisé. [8–10] Cette chaleur est absorbée par un fluide caloporteur à base d’eau. Lorsque le matériau magnétocalorique est démagnétisé, il se refroidit à sa température initiale, en supposant qu’il n’y ait pas de transfert de chaleur avec le fluide caloporteur. Dans le cas où le matériau magnétocalorique a échangé de la chaleur avec le fluide caloporteur pendant la magnétisation, le matériau magnétocalorique, en se refroidissant, absorbe la chaleur du fluide pendant la démagnétisation, générant ainsi un effet de refroidissement, comme le montre la figure 1.
Froid élastocalorique
Les matériaux élastocaloriques, tels que les alliages à mémoire de forme, par exemple le nitinol, ou les polymères, par exemple le caoutchouc naturel, sont chargés cycliquement en compression ou en tension. De la même manière que pour le froid magnétocalorique, le matériau élastocalorique génère un effet de chauffage/refroidissement [11–13]. En d’autres termes, lorsque le matériau élastocalorique est chargé assez rapidement, il génère de la chaleur qui peut être absorbée par le fluide caloporteur. Ensuite, pendant la phase de déchargement, le matériau élastocalorique se refroidit et absorbe la chaleur du fluide [14].
Froid électrocalorique
Un mince film de matériau électrocalorique, tel que des céramiques ou des polymères [15], est exposé à une variation périodique du champ électrique. La (dé)polarisation du matériau qui en résulte est à l’origine de l’effet de chauffage/refroidissement généré, qui peut être absorbé et transporté par un fluide caloporteur diélectrique ou par l’application de commutateurs thermiques [16]. En d’autres termes, lorsqu’un matériau électrocalorique est exposé à l’augmentation du potentiel électrique, il génère de la chaleur qui peut être absorbée par le fluide diélectrique ou un interrupteur thermique. Ensuite, pendant la décharge, le matériau électrocalorique se refroidit et absorbe la chaleur du fluide diélectrique ou de l’interrupteur thermique.
Froid barocalorique
Lorsqu’un matériau barocalorique est exposé à un changement périodique de pression hydrostatique, cela génère un effet de chauffage/refroidissement [17]. En d’autres termes, lorsque le matériau barocalorique est exposé à une augmentation de la pression hydrostatique, il génère de la chaleur qui peut être absorbée par le fluide caloporteur. Ensuite, lors de la décompression, le matériau barocalorique se refroidit et absorbe la chaleur du fluide.
Il convient de noter que récemment, l’effet dit multicalorique a suscité un intérêt accru de la part des chercheurs. Dans ce cas, un matériau multicalorique est exposé à la variation de deux champs ou plus. Par exemple, le matériau est d’abord (dé)magnétisé puis, pour augmenter encore sa réponse thermique, la pression hydrostatique est augmentée ou diminuée.
L’intérêt de la fabrication additive pour répondre aux défis du froid calorique
De nombreux défis doivent être relevés avant d’atteindre l’efficacité théorique escomptée pour le refroidissement calorique, malgré des prédictions de rendement exergétique élevé.[18] Ainsi, le principal défi du froid barocalorique est le transfert de chaleur entre le puits de chaleur et la source de chaleur via le matériau barocalorique sous pression cyclique [15] Pour le froid électrocalorique, le développement de matériaux plus efficaces est nécessaire.[16]
En ce qui concerne le froid magnétocalorique et élastocalorique, la géométrie du régénérateur représente l’un des problèmes les plus courants.[19–22] Il est préférable d’utiliser des régénérateurs permettant un transfert de chaleur rapide du solide vers le fluide caloporteur avec une chute de pression minimale. Ainsi, les géométries offrant un ratio élevé entre surface et volume sont préférables. Cependant, la fabrication de telles géométries à l’aide de techniques de fabrication conventionnelles est difficile, voire impossible. Ainsi, des travaux de recherche sont en cours pour développer un procédé de fabrication additive adapté à la fabrication de régénérateurs fonctionnels pour le refroidissement magnétocalorique et élastocalorique, avec les caractéristiques géométriques et la finition de surface requises.
À ce jour, seules quelques études ont été faites sur la fabrication additive de régénérateurs caloriques. Néanmoins, des résultats inspirants et prometteurs ont été obtenus, encourageant la poursuite de la recherche et l’optimisation des processus. Les dernières réalisations en matière de fabrication additive des régénérateurs caloriques et les défis les plus courants sont présentés ci-après.
Fabrication additive de régénérateurs caloriques
Fabrication additive de régénérateurs magnétocaloriques
En 2013, Moore et collègues [23] ont été les premiers à démontrer que la fusion laser sélective (SLM) pouvait être utilisée pour fabriquer des régénérateurs magnétocaloriques. Ils ont démontré que les structures internes ondulées destinées à augmenter le transfert de chaleur pouvaient être fabriquées avec succès à partir d'un matériau à transition de phase de second ordre à base de LaFe10.7Co1.3Si. Après le processus SLM, les structures fabriquées ont dû être recuites afin d'obtenir la phase magnétocalorique 1:13. Néanmoins, après le recuit, les structures fabriquées ont été exposées à l'air et se sont désintégrées en 24 heures.
D'autres tentatives de fabrication additive d'échantillons magnétocaloriques ont également été effectuées par dépôt de matière sous énergie concentrée [24] et par projection de liant [25]. Les études ont montré que les propriétés magnétocaloriques des échantillons produits par fabrication additive pouvaient être obtenues après des processus de frittage et/ou de recuit et étaient comparables à celles des pièces fabriquées à l'aide de technologies conventionnelles. Il a également été démontré que le développement de fissures est corrélé à la densité d'énergie appliquée pour la fabrication d'échantillons magnétocaloriques [24].
Dans une étude récente, des matériaux magnétocaloriques à transition de phase de premier ordre ont été fabriqués de manière additive, par fusion laser sélective (SLM) [26]. Les auteurs ont démontré que les propriétés magnétocaloriques des échantillons recuits étaient au moins 3 fois supérieures à celles du gadolinium de référence.
En 2020, Navickaitė et collègues ont publié la première étude démontrant les performances de régénérateurs magnétocaloriques de grande taille fabriqués à partir d'un matériau de second ordre à base de LaCe(FeSiMn)H, dans un cycle thermomagnétique [27]. Dans cette étude, des régénérateurs avec des motifs d'écoulement inspirés de la nature ont été fabriqués de manière additive par fusion par faisceau laser (LBM). Après le processus LBM, les échantillons ont été traités thermiquement pour obtenir la phase magnétocalorique 1:13, puis hydrogénés. Les essais à long terme ont démontré qu’il est possible de produire des régénérateurs magnétocaloriques mécaniquement stables et entièrement fonctionnels avec des géométries complexes, lorsque les paramètres de fabrication additive adéquats sont employés (tels que la puissance du laser, la vitesse de balayage, la taille de la trappe, etc.). Cependant, les auteurs de l'étude ont également conclu qu’il est nécessaire d’optimiser le traitement thermique et le processus d'hydrogénation, ainsi que de développer des technologies de fabrication additive permettant d’obtenir des structures plus fines.
Il convient de souligner que la qualité des régénérateurs fabriqués de manière additive dépend également de la taille initiale de la poudre utilisée. Une poudre plus fine permet de fabriquer des pièces avec une meilleure qualité de surface et une porosité plus faible. Cependant, la poudre doit toujours avoir une bonne fluidité, ce qui affecte également la qualité des pièces finales. Malheureusement, les poudres magnétocaloriques ont généralement une fluidité inférieure à celle des poudres métalliques conventionnelles de même taille.
Fabrication additive de régénérateurs élastocaloriques
Le matériau élastocalorique le plus couramment étudié est le Nitinol quasi-équiatomique. Le Nitinol est un alliage de nickel et titane. Jusqu'à présent, seules des géométries conventionnelles, telles que des fils, des tubes et des plaques, ont été utilisées pour construire des régénérateurs destinés à des études expérimentales dans des machines d'essais élastocaloriques [14, 28, 29]. Les régénérateurs en fil et en plaque ont été testés sous une charge de traction, tandis que les tubes ont été chargés en compression, en veillant à ce qu'ils ne se déforment pas.
Le choix des géométries pour le refroidissement élastocalorique est quelque peu limité non seulement par les possibilités de fabrication offertes par les technologies traditionnelles, mais aussi par les conditions de chargement du régénérateur et les défis d’ingénierie. Premièrement, la géométrie utilisée doit permettre une disposition simple du système hydraulique qui n'interfère pas avec les poignées mécaniques. Deuxièmement, les régénérateurs exploités sous une charge de traction doivent avoir une faible section transversale afin de réduire la force minimale appliquée nécessaire pour induire l'effet élastocalorique. D'autre part, les géométries des régénérateurs chargés en compression doivent être conçues de manière à éviter le flambage, car aucun effet élastocalorique ne peut être induit si les régénérateurs se déforment [30].
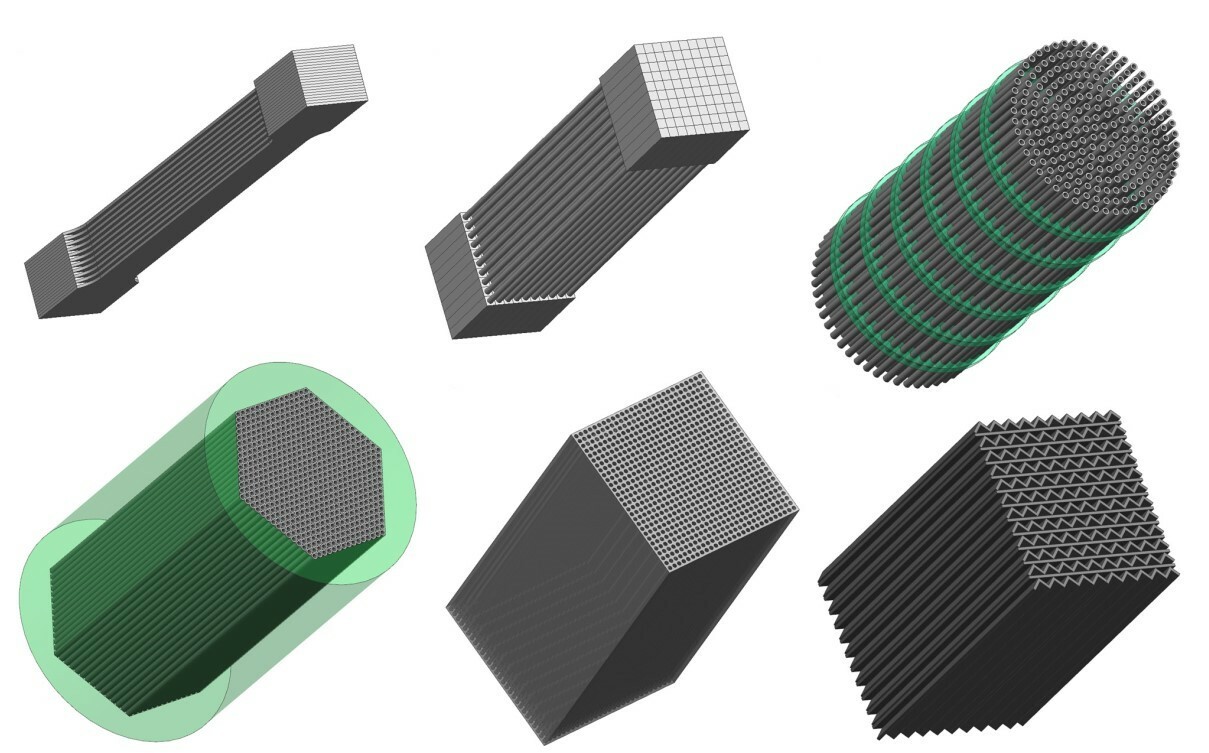
La résistance à la fatigue est un autre défi des matériaux élastocaloriques. Il a été démontré que l'état de surface du matériau a un impact direct sur la résistance à la fatigue, et donc sur la durée de vie des régénérateurs élastocaloriques [31]. En effet, une rugosité de surface élevée provoque un développement de fissures sous charge de traction et compromet ainsi la fonctionnalité des régénérateurs élastocaloriques [30]. Par conséquent, un polissage supplémentaire de la surface des régénérateurs élastocaloriques fabriqués de manière additive est nécessaire [32].
En plus des défis susmentionnés, le Nitinol, est très difficile à usiner, principalement en raison de la forte réactivité du titane. Ainsi, la fabrication additive du Nitinol est un processus très difficile. Il a été démontré qu'en raison de la réactivité élevée du titane et de la température d'évaporation relativement basse du nickel, la température de transition de phase des pièces finales peut être différente de celle des poudres brutes [33], ce qui affecte la plage de température de fonctionnement. Néanmoins, certaines études ont mis en évidence des propriétés élastocaloriques pertinentes pour le fonctionnement dans des échantillons de nitinol fabriqués de manière additive par dépôt de matière sous énergie concentrée [34, 35]. Cependant, ces échantillons en vrac n'ont pas été testés dans un dispositif d'essai élastocalorique actif pour déterminer leurs performances thermomécaniques.
Liens utiles pour plus d’informations
-
Notes d'Information IIF
Magnetic refrigeration at room temperature, 20th IIR Informatory Note on Refrigerating Technologies (2007). https://iifiir.org/en/fridoc/magnetic-refrigeration-at-room-temperature-20-lt-sup-gt-th-lt-sup-gt-iir-128806
-
Articles de la Revue Internationale du Froid
Torelló, À., & Defay, E. (2021). Heat exchange law in caloric regenerators. International Journal of Refrigeration, 127, 174-179. https://iifiir.org/en/fridoc/heat-exchange-law-in-caloric-regenerators-143547
Tušek, J., Kitanovski, A., & Poredoš, A. (2013). Geometrical optimization of packed-bed and parallel-plate active magnetic regenerators. International Journal of Refrigeration, 36(5), 1456-1464. https://iifiir.org/en/fridoc/geometrical-optimization-of-packed-bed-and-parallel-plate-active-136251
Gschneidner Jr, K. A., & Pecharsky, V. K. (2008). Thirty years of near room temperature magnetic cooling: Where we are today and future prospects. International journal of refrigeration, 31(6), 945-961. https://iifiir.org/en/fridoc/thirty-years-of-near-room-temperature-magnetic-cooling-where-we-are-130171
-
Documents de conference
9th IIR Conference on Caloric Cooling and Applications of Caloric Materials (Thermag 2021) https://iifiir.org/en/fridoc/9-lt-sup-gt-th-lt-sup-gt-iir-conference-on-caloric-cooling-and-applications-of-143528
Thermag - IIR Conference on Caloric Cooling and Applications of Caloric Materials https://iifiir.org/en/fridoc/thermag-iir-conference-on-caloric-cooling-and-applications-of-caloric-67
-
Articles open access
Greco, A., & Masselli, C. (2020). Electrocaloric cooling: a review of the thermodynamic cycles, materials, models, and devices. Magnetochemistry, 6(4), 67. https://iifiir.org/en/fridoc/electrocaloric-cooling-a-review-of-the-thermodynamic-cycles-142901
Engelbrecht, K. (2019). Future prospects for elastocaloric devices. Journal of Physics: Energy, 1(2), 021001. https://doi.org/10.1088/2515-7655/ab1573
Remerciements
Ce document de synthèse a été préparé par Dr Kristina NAVICKAITE, membre junior de la commission E1 « Conditionnement d’air ».
Il a été mis en page et traduit en français par Monique Baha (siège de l'IIF). Il a été relu par Nathalie de Grissac et Zoé Martin, sous la supervision de Jean-Luc Dupont (Responsable du Département d'Information Scientifique et Technique).
Références
[1] “7 types of additive manufacturing,” Applied Engineering, 2020. https://www.appliedengineering.com/blog/2021/1/22/7-types-of-additive-manufacturing (accessed Dec. 27, 2021).
[2] K. N. Al-Milaji, S. Gupta, V. K. Pecharsky, R. Barua, H. Zhao, and R. L. Hadimani, “Differential effect of magnetic alignment on additive manufacturing of magnetocaloric particles,” AIP Adv., vol. 10, no. 1, p. 015052, Jan. 2020, doi: 10.1063/1.5130028.
[3] M. R. Burton et al., “3D Printed SnSe Thermoelectric Generators with High Figure of Merit,” Adv. Energy Mater., vol. 9, no. 26, 2019, doi: 10.1002/aenm.201900201.
[4] T. N. Tran et al., “Cocoa Shell Waste Biofilaments for 3D Printing Applications,” Macromol. Mater. Eng., vol. 302, no. 11, pp. 1–10, 2017, doi: 10.1002/mame.201700219.
[5] N. Narioglu, T. Salan, and M. H. Alma, “Properties of 3D-Printed Wood Sawdust-Reinforced PLA Composites,” BioResources, vol. 16, no. 3, pp. 5467-5480., 2021.
[6] E. M. Palmero et al., “Composites based on metallic particles and tuned filling factor for 3D-printing by Fused Deposition Modeling,” Compos. Part A Appl. Sci. Manuf., vol. 124, no. November 2018, p. 105497, 2019, doi: 10.1016/j.compositesa.2019.105497.
[7] T. DebRoy et al., “Additive manufacturing of metallic components – Process, structure and properties,” Prog. Mater. Sci., vol. 92, pp. 112–224, 2018, doi: 10.1016/j.pmatsci.2017.10.001.
[8] A. Smith, C. R. H. Bahl, R. Bjørk, K. Engelbrecht, K. K. Nielsen, and N. Pryds, “Materials challenges for high performance magnetocaloric refrigeration devices,” Adv. Energy Mater., vol. 2, no. 11, 2012, doi: 10.1002/aenm.201200167.
[9] G. V. Brown, “Magnetic heat pump.,” NASA Conf. Publ., 1980.
[10] V. K. Pecharsky and K. A. Gschneidner, “Magnetocaloric effect and magnetic refrigeration,” J. Magn. Magn. Mater., vol. 200, no. 1–3, 1999, doi: 10.1016/S0304-8853(99)00397-2.
[11] J. Tušek et al., “The elastocaloric effect : a way to cool efficiently,” Adv. Energy Mater., vol. 5, 2015, doi: 10.1002/aenm.201500361.
[12] K. Engelbrecht, “Future prospects for elastocaloric devices,” J. Phys. Energy, vol. 1, no. 2, p. 021001, May 2019, doi: 10.1088/2515-7655/ab1573.
[13] E. Bonnot, R. Romero, L. Mañosa, E. Vives, and A. Planes, “Elastocaloric effect associated with the martensitic transition in shape-memory alloys,” Phys. Rev. Lett., vol. 100, no. 12, 2008, doi: 10.1103/PhysRevLett.100.125901.
[14] J. Tušek, K. Engelbrecht, L. P. Mikkelsen, and N. Pryds, “Elastocaloric effect of Ni-Ti wire for application in a cooling device,” J. Appl. Phys., vol. 117, no. 12, 2015, doi: 10.1063/1.4913878.
[15] X. Moya and N. D. Mathur, “Caloric materials for cooling and heating,” Science (80-. )., vol. 370, pp. 797–803, 2020.
[16] Y. Wang et al., “A high-performance solid-state electrocaloric cooling system,” Science (80-. )., vol. 370, pp. 129–133, 2020.
[17] A. Kitanovski, J. Tušek, U. Tomc, U. Plaznik, M. Ožbolt, and A. Poredoš, Magnetocaloric Energy Conversion. Cham: Springer International Publishing, 2015.
[18] K. A. Gschneidner and V. K. Pecharsky, “Thirty years of near room temperature magnetic cooling: Where we are today and future prospects,” Int. J. Refrig., vol. 31, no. 6, pp. 945–961, 2008, doi: 10.1016/j.ijrefrig.2008.01.004.
[19] J. Tušek, A. Kitanovski, and A. Poredoš, “Geometrical optimization of packed-bed and parallel-plate active magnetic regenerators,” Int. J. Refrig., vol. 36, no. 5, 2013, doi: 10.1016/j.ijrefrig.2013.04.001.
[20] K. Navickaitė, C. R. H. Bahl, and K. Engelbrecht, “Nature-inspired flow patterns for active magnetic regenerators assessed using a 1D AMR model,” Front. Energy Res., vol. 7, pp. 1–17, Jul. 2019, doi: 10.3389/fenrg.2019.00068.
[21] J. Liang, C. D. Christiansen, K. Engelbrecht, K. K. Nielsen, R. Bjørk, and C. R. H. Bahl, “Characterization of Freeze-Cast Micro-Channel Monoliths as Active and Passive Regenerators,” Front. Energy Res., vol. 8, Apr. 2020, doi: 10.3389/fenrg.2020.00054.
[22] T. Lei, K. Engelbrecht, K. K. Nielsen, and C. T. Veje, “Study of geometries of active magnetic regenerators for room temperature magnetocaloric refrigeration,” Appl. Therm. Eng., vol. 111, 2017, doi: 10.1016/j.applthermaleng.2015.11.113.
[23] J. D. Moore et al., “Selective laser melting of La(Fe,Co,Si) 13 geometries for magnetic refrigeration,” J. Appl. Phys., vol. 114, no. 4, p. 043907, Jul. 2013, doi: 10.1063/1.4816465.
[24] B. T. Lejeune, X. Du, R. Barua, J. C. Zhao, and L. H. Lewis, “Anisotropic thermal conductivity of magnetocaloric AlFe2B2,” Materialia, vol. 1, no. May, pp. 150–154, 2018, doi: 10.1016/j.mtla.2018.05.011.
[25] A. Mostafaei, P. R. De Vecchis, E. L. Stevens, and M. Chmielus, “Sintering regimes and resulting microstructure and properties of binder jet 3D printed Ni-Mn-Ga magnetic shape memory alloys,” Acta Mater., vol. 154, pp. 355–364, 2018, doi: 10.1016/j.actamat.2018.05.047.
[26] X. Miao et al., “Printing (Mn,Fe)2(P,Si) magnetocaloric alloys for magnetic refrigeration applications,” J. Mater. Sci., vol. 55, no. 15, pp. 6660–6668, 2020, doi: 10.1007/s10853-020-04488-8.
[27] K. Navickaitė, J. Liang, C. R. H. Bahl, S. Wieland, T. Buchenau, and K. Engelbrecht, “Experimental characterization of active magnetic regenerators constructed using laser beam melting technique,” Appl. Therm. Eng., vol. 174, p. 115297, 2020, doi: 10.1016/j.applthermaleng.2020.115297.
[28] J. Tušek, K. Engelbrecht, D. Eriksen, S. Dall’Olio, J. Tušek, and N. Pryds, “A regenerative elastocaloric heat pump,” Nat. Energy, vol. 1, no. 10, 2016, doi: 10.1038/nenergy.2016.134.
[29] D. Catalini, N. Emaikwu, Y. Hwang, R. Radermacher, and I. Takeuchi, “Elastocaloric Cooling,” vol. 37, no. 3, pp. 29–32, 2019.
[30] P. Kabirifar, A. Žerovnik, Ž. Ahčin, L. Porenta, M. Brojan, and J. Tušek, “Elastocaloric Cooling: State-of-the-art and Future Challenges in Designing Regenerative Elastocaloric Devices,” Strojniški Vestn. – J. Mech. Eng., vol. 65, no. 11–12, pp. 615–630, Nov. 2019, doi: 10.5545/sv-jme.2019.6369.
[31] K. Engelbrecht et al., “Effects of surface finish and mechanical training on Ni-Ti sheets for elastocaloric cooling,” APL Mater., vol. 4, no. 6, p. 064110, Jun. 2016, doi: 10.1063/1.4955131.
[32] K. Navickaitė et al., “Plasma electrolytic polishing of Nitinol : Investigation of functional properties,” Materials (Basel)., vol. 14, p. 6450, 2021, doi: 10.3390/ma14216450.
[33] M. T. Andani, C. Haberland, J. Walker, and M. Elahinia, “An Investigation of Effective Process Parameters on Phase Transformation Temperature of Nitinol Manufactured by Selective Laser Melting,” in Proceedings of the ASME 2014 Conference on Smart Materials, Adaptive Structures and Intelligent Systems, Sep. 2014, pp. 1–5, doi: 10.1115/SMASIS2014-7649.
[34] H. Hou et al., “Elastocaloric cooling of additive manufactured shape memory alloys with large latent heat,” J. Phys. D. Appl. Phys., vol. 50, no. 40, 2017, doi: 10.1088/1361-6463/aa85bf.
[35] H. Hou et al., “Fatigue-resistant high-performance elastocaloric materials made by additive manufacturing,” Science (80-. )., vol. 366, no. 6469, pp. 1116–1121, 2019, doi: 10.1126/science.aax7616.
Crédit image (à des fins d'illustration): Oak Ridge National Laboratory. Polymer Additive Manufacturing lab at the Manufacturing Demonstration Facility. https://flic.kr/p/ePhuYa
Rechercher dans l'encyclopédie les articles sur le thème suivant :
Cryogénie et traitement des gaz | Frigorigènes et frigoporteurs | Equipements frigorifiques | Cryobiologie et cryomédecine, lyophilisation | Application du froid aux produits périssables | Entreposage frigorifique | Pompes à chaleur, récupération d'énergie | Généralités sur le froid, l'énergie et l'environnement