Additive manufacturing of regenerators for caloric cooling
In many areas of engineering, additive manufacturing allows the production of complex and multifunctional products that could not be manufactured using traditional methods. In the field of caloric cooling, additive manufacturing allows the optimisation of regenerator geometry, thus improving the performance of magnetocaloric and elastocaloric cooling technologies in particular. This summary document presents the basics of additive manufacturing processes, the different types of caloric cooling, and the advances in research on the additive manufacturing of caloric regenerators.
What is additive manufacturing?
The term “additive manufacturing” embraces a number of different technologies that allow goods to be manufactured additively. This means that instead of subtracting material from a bulk piece, as is done in conventional manufacturing processes such as cutting and milling, material is added layer by layer to form the desired product. Note that additive manufacturing is more commonly known as 3D printing.
Seven types of additive manufacturing processes
There are several distinct types of additive manufacturing processes based on some key characteristics [1].
- Material jetting (MJ). Here, a material is deposited on a substrate in the form of droplets to form layers of printed material. This additive manufacturing method is particularly favoured for manufacturing thin films [2, 3].
- Stereolithography. In this process, a liquid plastic is hardened by a UV light-emitting laser beam to obtain a very detailed 3D geometry. This method cannot be used for metal processing.
- Binder jetting (BJ). The material particles are bound using a liquid binder to form the desired part. The binder jetting process is rather fast and does not involve any high temperature process. Nevertheless, if metal parts with relatively good mechanical properties are to be produced, a post-processing heat treatment is required to sinter the metal particles and burn the binder.
- Material extrusion (ME). Here, the material is extruded layer-by-layer from a heated nozzle to form a final object. This is probably the most popular additive manufacturing technology, since material extruding printers are rather cheap. The most common materials used in this technique are plastic filaments, but composite materials, e.g. saw dust or cocoa shell waste bound with a biodegradable plastic [4, 5], metal powder bound with a suitable polymer [6], etc., are also available.
- Powder bed fusion (PBF). Here, the material, a metal or polymer powder is spread over a built platform in a thin layer using a coater. Then the material is selectively melted or sintered by a laser or electron beam. Another thin layer of the material is then applied and the process is repeated until the desired part is fabricated. The surface quality and mechanical properties of the parts produced highly depend on the applied energy density, scanning speed, hatch strategy and, of course, powder size and morphology [7]. Some of the most commonly used materials for PBF are nylon, aluminium, steel, titanium and copper.
- Sheet lamination (SL). Here, sheets of material are bound together either by ultrasonic welding or by applying an adhesive. SL allows different materials to be bound together. The final shape of the laminated sheets is cut with a knife or laser.
- Direct energy deposition (DED). This is a very complex additive manufacturing process in which multiple arms move around a fixed object and deposit a material that is then melted by a laser or electron beam. The most popular materials for DED are metal wires and/or powders.
Naturally, certain additive manufacturing techniques are more suitable for specific applications than others. Therefore, in this document, the focus will be on techniques that have already been applied to fabricate regenerators for caloric cooling applications.
What is caloric cooling?
Caloric cooling is an environmentally friendly alternative to vapour compression technology. In caloric cooling, solid-state porous/permeable regenerators are used for generating a heating/cooling effect. There are four types of caloric cooling: magnetocaloric, elastocaloric, electrocaloric, barocaloric.
The principle of single-cause caloric cooling and its comparison with vapour compression technology is provided in Figure 1 and summarised in Table 1, where the term “field change” is used to unify the change of magnetic, electric and mechanical fields.
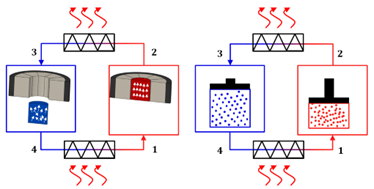
Table 1. A comparison of caloric cooling and vapour compression processes during a cooling cycle.
Process No. | Caloric cooling | Vapour compression |
---|---|---|
1 - 2 | Adiabatic field change | Isentropic compression |
2 - 3 | Constant field heat rejection to the heat sink | Constant pressure heat rejection in the condenser |
3 - 4 | Adiabatic field change | Throttling in an expansion valve |
4 - 1 | Constant field heat absorption from the heat source | Constant pressure heat absorption in the evaporator |
Magnetocaloric cooling
Here, magnetocaloric materials, such as gadolinium and its alloys or LaFeSi family alloys, are exposed to a periodic change in the external magnetic field. This causes changes in material lattice, resulting in heat generation when the material is magnetised [8–10]. This heat is absorbed by a timely flow of water-based heat transfer fluid (HTF). When the magnetocaloric material is demagnetised, it cools down to its initial temperature, assuming there is no heat transfer with the HTF. In case the magnetocaloric material has exchanged heat with the HTF during magnetisation, the magnetocaloric material absorbs heat from the HTF during the demagnetisation, thus generating a cooling effect, as shown in Figure 1.
Elastocaloric cooling
Here, elastocaloric materials, such as shape memory alloys, e.g., Nitinol, or polymers such as natural rubber, are cyclically loaded in compression or tension. This, similarly to magnetocaloric cooling, results in the elastocaloric material generating a heating/cooling effect [11–13]. In other words, when the elastocaloric material is loaded fast enough, it generates heat that can be absorbed by the heat transfer fluid. Then, during the unloading phase, the elastocaloric material cools down and absorbs the heat from the heat transfer fluid [14].
Electrocaloric cooling
Here, a thin film of electrocaloric material, such as ceramics or polymers [15], is exposed to a periodic change in electric field. The resulting (de)polarisation of the material is the cause of the generated heating/cooling effect, which can be absorbed and transported by a dielectric heat transfer fluid or by the application of thermal switches [16]. In other words, when the electrocaloric material is exposed to the increase in electrical potential, it generates heat that can be absorbed by the dielectric heat transfer fluid or a thermal switch, and then during the discharge, the electrocaloric material cools down and absorbs the heat from the dielectric heat transfer fluid or a thermal switch.
Barocaloric cooling
Here, a barocaloric material is exposed to a periodic change in hydrostatic pressure, which generates a heating/cooling effect [17]. In other words, when the barocaloric material is exposed to an increase in hydrostatic pressure, it generates heat that can be absorbed by the heat transfer fluid. Then, upon decompression, the barocaloric material cools down and absorbs the heat from the heat transfer fluid.
It should be noted that recently, the so-called multicaloric effect has gained increased interest from researchers. Here, a multicaloric material is exposed to the change of two or more fields, e.g., the material is first (de)magnetised and then, to further increase its thermal response, the hydrostatic pressure is increased/decreased.
The potential of additive manufacturing to adress the challenges of caloric cooling
Despite predictions of high exergy efficiency for caloric cooling [18], many challenges must be addressed in order to achieve the anticipated theoretical efficiency. The main challenge in barocaloric cooling is the heat transfer between the heat sink and the heat source via cyclically pressurised barocaloric material [15]. For electrocaloric cooling, the development of more efficient materials is required [16].
For magnetocaloric and elastocaloric cooling, the regenerator geometry is one of the most common problems [19–22]. It is preferable to use regenerators enabling fast heat transfer from the solid to the heat transfer fluid with minimal pressure drop. Thus, geometries with high surface-to-volume ratio are preferred. However, manufacturing such geometries using conventional fabrication techniques is challenging, if not impossible. Thus, research efforts are ongoing to develop additive manufacturing processes suitable for the manufacturing of functional regenerators for magneto- and elastocaloric cooling, with the required geometrical features and surface finish.
To date, only a few studies have been reported on additive manufacturing of caloric regenerators. Nevertheless, inspiring and promising results have been obtained, encouraging further research and process optimisation. The latest achievements in additive manufacturing of caloric regenerators and the most common challenges are presented below.
Additive manufactured caloric regenerators
Additive manufactured magnetocaloric regenerators
In 2013, Moore et al. were the first to demonstrate that selective laser melting (SLM) could be used for manufacturing magnetocaloric regenerators [23]. They proved that wavy inner structures designed to increase heat transfer could be successfully manufactured from second-order phase transition LaFe10.7Co1.3Si material. After the SLM process, the manufactured structures had to be annealed in order to obtain the magnetocaloric 1:13 phase. Nevertheless, after annealing, the manufactured structures were exposed to air and disintegrated within 24 hours.
Other attempts to produce magnetocaloric samples using DED [24] and BJ [25] have also been made. It was shown that the magnetocaloric properties of additive manufactured samples could be obtained after sintering and/or annealing processes and were comparable to those of the parts made using conventional technologies. It has also been shown that the development of cracks correlates with the energy density applied for the manufacturing of magnetocaloric samples [24].
Recently, the SLM process was used to additively manufacture magnetocaloric materials with the first-order phase transition [26]. The authors demonstrated that the magnetocaloric properties of the annealed samples were at least 3 times higher than that of benchmark gadolinium.
In 2020, Navickaitė et al. published the first study demonstrating the performance of full-size magnetocaloric regenerators produced from second-order LaCe(FeSiMn)H material under thermo-magnetic cycle [27]. In this study, regenerators with nature-inspired flow patterns were additively manufactured using the laser beam melting (LBM) technique. After the LBM process, the samples were heat treated to gain the magnetocaloric 1:13 phase and then hydrogenated. The long-term testing has demonstrated that it is possible to produce mechanically stable and fully functional magnetocaloric regenerators with complex geometries by using the right additive manufacturing parameters, such as laser power, scan speed, hatch size etc. However, the authors of the study also concluded that optimising the heat treatment and hydrogenation process is necessary, as well as further development of AM technologies to create finer structures.
It must be emphasised that the quality of additive manufactured regenerators also depends on the initial powder size. A finer powder size enables the manufacturing of parts with a better surface quality and lower porosity. However, the powder should still have good flowability, which also affects the quality of the final parts. Unfortunately, magnetocaloric powders usually have lower flowability compared to conventional metal powders of the same particle size.
Additive manufactured elastocaloric regenerators
The most commonly investigated elastocaloric material is near-equiatomic Nitinol. Nitinol is a metal alloy of nickel and titanium. So far, only conventional geometries, such as wires, tubes and plates, have been used to construct regenerators for experimental investigations in elastocaloric testing machines [14, 28, 29]. Wire and plate regenerators have been tested under tensile loading, while tubes have been loaded in compression, ensuring that they did not buckle.
The choice of geometries for elastocaloric cooling is somewhat limited not only by the manufacturing possibilities offered by conventional technologies, but also by regenerator loading conditions and engineering challenges. Firstly, the geometry used must enable a simple arrangement of the hydraulic system that does not interfere with the mechanical grips. Secondly, regenerators exploited under tensile load must have a small cross-section area in order to reduce the minimum applied force required to induce the elastocaloric effect. On the other hand, the geometries of regenerators loaded in compression should be designed so as to avoid buckling, since no elastocaloric effect is induced if the regenerators buckle [30].
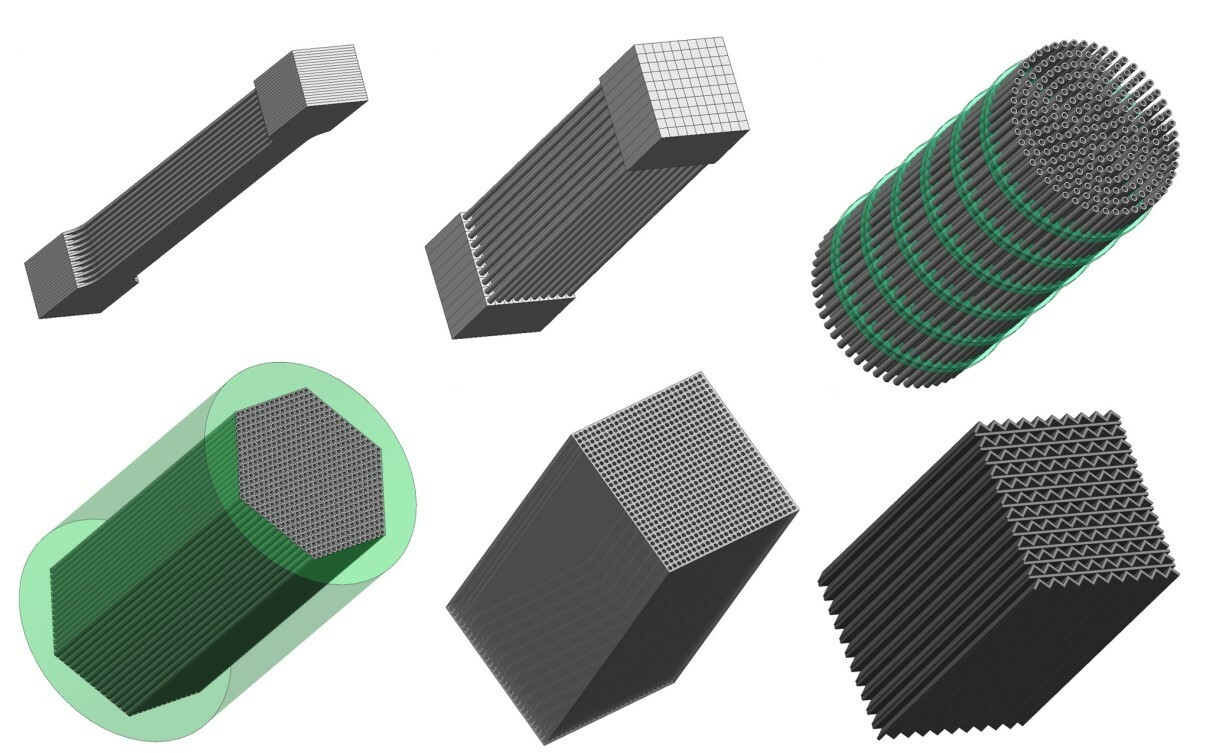
Another challenge presented by elastocaloric materials is their fatigue resistance. It has been demonstrated that the surface finish of the elastocaloric material has a direct impact on the fatigue resistance, and thus on service life of the elastocaloric regenerators [31]. Indeed, high surface roughness causes a crack development under tensile loading and thus compromises the functionality of elastocaloric regenerators [30]. Therefore, additional surface polishing of additively manufactured elastocaloric regenerators is required [32].
In addition to the aforementioned challenges, Nitinol is very difficult to machine, mainly due to the high reactivity of titanium. Thus, additive manufacturing of Nitinol is a very challenging process. It has been demonstrated that, due to high reactivity of titanium and the relatively low evaporation temperature of nickel, the phase transition temperature of the final parts might be different than that of the raw powders [33], thus affecting the operating temperature range. Nevertheless, some studies have demonstrated that operation-relevant elastocaloric properties could be recovered in Nitinol samples manufactured using DED [34, 35]. However, these samples are in bulk and have not been examined in an active elastocaloric testing device to characterise their thermo-mechanical performance.
Useful links for further information
-
IIR Informatory Note
Magnetic refrigeration at room temperature, 20th IIR Informatory Note on Refrigerating Technologies (2007). https://iifiir.org/en/fridoc/magnetic-refrigeration-at-room-temperature-20-lt-sup-gt-th-lt-sup-gt-iir-128806
-
Articles from the International Journal of Refrigeration
Torelló, À., & Defay, E. (2021). Heat exchange law in caloric regenerators. International Journal of Refrigeration, 127, 174-179. https://iifiir.org/en/fridoc/heat-exchange-law-in-caloric-regenerators-143547
Tušek, J., Kitanovski, A., & Poredoš, A. (2013). Geometrical optimization of packed-bed and parallel-plate active magnetic regenerators. International Journal of Refrigeration, 36(5), 1456-1464. https://iifiir.org/en/fridoc/geometrical-optimization-of-packed-bed-and-parallel-plate-active-136251
Gschneidner Jr, K. A., & Pecharsky, V. K. (2008). Thirty years of near room temperature magnetic cooling: Where we are today and future prospects. International journal of refrigeration, 31(6), 945-961. https://iifiir.org/en/fridoc/thirty-years-of-near-room-temperature-magnetic-cooling-where-we-are-130171
-
Conference papers
9th IIR Conference on Caloric Cooling and Applications of Caloric Materials (Thermag 2021) https://iifiir.org/en/fridoc/9-lt-sup-gt-th-lt-sup-gt-iir-conference-on-caloric-cooling-and-applications-of-143528
Thermag - IIR Conference on Caloric Cooling and Applications of Caloric Materials https://iifiir.org/en/fridoc/thermag-iir-conference-on-caloric-cooling-and-applications-of-caloric-67
-
Open access articles
Greco, A., & Masselli, C. (2020). Electrocaloric cooling: a review of the thermodynamic cycles, materials, models, and devices. Magnetochemistry, 6(4), 67. https://iifiir.org/en/fridoc/electrocaloric-cooling-a-review-of-the-thermodynamic-cycles-142901
Engelbrecht, K. (2019). Future prospects for elastocaloric devices. Journal of Physics: Energy, 1(2), 021001. https://doi.org/10.1088/2515-7655/ab1573
Acknowledgements
This summary document was prepared by Dr Kristina NAVICKAITE, junior member of the E1 commission on “Air conditioning”. It was designed and translated into French by Monique Baha (IIR head office). It was proofread by Nathalie de Grissac and Zoé Martin, under the supervision of Jean-Luc Dupont (Head of the Scientific and Technical Information Department).
References
[1] “7 types of additive manufacturing,” Applied Engineering, 2020. https://www.appliedengineering.com/blog/2021/1/22/7-types-of-additive-manufacturing (accessed Dec. 27, 2021).
[2] K. N. Al-Milaji, S. Gupta, V. K. Pecharsky, R. Barua, H. Zhao, and R. L. Hadimani, “Differential effect of magnetic alignment on additive manufacturing of magnetocaloric particles,” AIP Adv., vol. 10, no. 1, p. 015052, Jan. 2020, doi: 10.1063/1.5130028.
[3] M. R. Burton et al., “3D Printed SnSe Thermoelectric Generators with High Figure of Merit,” Adv. Energy Mater., vol. 9, no. 26, 2019, doi: 10.1002/aenm.201900201.
[4] T. N. Tran et al., “Cocoa Shell Waste Biofilaments for 3D Printing Applications,” Macromol. Mater. Eng., vol. 302, no. 11, pp. 1–10, 2017, doi: 10.1002/mame.201700219.
[5] N. Narioglu, T. Salan, and M. H. Alma, “Properties of 3D-Printed Wood Sawdust-Reinforced PLA Composites,” BioResources, vol. 16, no. 3, pp. 5467-5480., 2021.
[6] E. M. Palmero et al., “Composites based on metallic particles and tuned filling factor for 3D-printing by Fused Deposition Modeling,” Compos. Part A Appl. Sci. Manuf., vol. 124, no. November 2018, p. 105497, 2019, doi: 10.1016/j.compositesa.2019.105497.
[7] T. DebRoy et al., “Additive manufacturing of metallic components – Process, structure and properties,” Prog. Mater. Sci., vol. 92, pp. 112–224, 2018, doi: 10.1016/j.pmatsci.2017.10.001.
[8] A. Smith, C. R. H. Bahl, R. Bjørk, K. Engelbrecht, K. K. Nielsen, and N. Pryds, “Materials challenges for high performance magnetocaloric refrigeration devices,” Adv. Energy Mater., vol. 2, no. 11, 2012, doi: 10.1002/aenm.201200167.
[9] G. V. Brown, “Magnetic heat pump.,” NASA Conf. Publ., 1980.
[10] V. K. Pecharsky and K. A. Gschneidner, “Magnetocaloric effect and magnetic refrigeration,” J. Magn. Magn. Mater., vol. 200, no. 1–3, 1999, doi: 10.1016/S0304-8853(99)00397-2.
[11] J. Tušek et al., “The elastocaloric effect : a way to cool efficiently,” Adv. Energy Mater., vol. 5, 2015, doi: 10.1002/aenm.201500361.
[12] K. Engelbrecht, “Future prospects for elastocaloric devices,” J. Phys. Energy, vol. 1, no. 2, p. 021001, May 2019, doi: 10.1088/2515-7655/ab1573.
[13] E. Bonnot, R. Romero, L. Mañosa, E. Vives, and A. Planes, “Elastocaloric effect associated with the martensitic transition in shape-memory alloys,” Phys. Rev. Lett., vol. 100, no. 12, 2008, doi: 10.1103/PhysRevLett.100.125901.
[14] J. Tušek, K. Engelbrecht, L. P. Mikkelsen, and N. Pryds, “Elastocaloric effect of Ni-Ti wire for application in a cooling device,” J. Appl. Phys., vol. 117, no. 12, 2015, doi: 10.1063/1.4913878.
[15] X. Moya and N. D. Mathur, “Caloric materials for cooling and heating,” Science (80-. )., vol. 370, pp. 797–803, 2020.
[16] Y. Wang et al., “A high-performance solid-state electrocaloric cooling system,” Science (80-. )., vol. 370, pp. 129–133, 2020.
[17] A. Kitanovski, J. Tušek, U. Tomc, U. Plaznik, M. Ožbolt, and A. Poredoš, Magnetocaloric Energy Conversion. Cham: Springer International Publishing, 2015.
[18] K. A. Gschneidner and V. K. Pecharsky, “Thirty years of near room temperature magnetic cooling: Where we are today and future prospects,” Int. J. Refrig., vol. 31, no. 6, pp. 945–961, 2008, doi: 10.1016/j.ijrefrig.2008.01.004.
[19] J. Tušek, A. Kitanovski, and A. Poredoš, “Geometrical optimization of packed-bed and parallel-plate active magnetic regenerators,” Int. J. Refrig., vol. 36, no. 5, 2013, doi: 10.1016/j.ijrefrig.2013.04.001.
[20] K. Navickaitė, C. R. H. Bahl, and K. Engelbrecht, “Nature-inspired flow patterns for active magnetic regenerators assessed using a 1D AMR model,” Front. Energy Res., vol. 7, pp. 1–17, Jul. 2019, doi: 10.3389/fenrg.2019.00068.
[21] J. Liang, C. D. Christiansen, K. Engelbrecht, K. K. Nielsen, R. Bjørk, and C. R. H. Bahl, “Characterization of Freeze-Cast Micro-Channel Monoliths as Active and Passive Regenerators,” Front. Energy Res., vol. 8, Apr. 2020, doi: 10.3389/fenrg.2020.00054.
[22] T. Lei, K. Engelbrecht, K. K. Nielsen, and C. T. Veje, “Study of geometries of active magnetic regenerators for room temperature magnetocaloric refrigeration,” Appl. Therm. Eng., vol. 111, 2017, doi: 10.1016/j.applthermaleng.2015.11.113.
[23] J. D. Moore et al., “Selective laser melting of La(Fe,Co,Si) 13 geometries for magnetic refrigeration,” J. Appl. Phys., vol. 114, no. 4, p. 043907, Jul. 2013, doi: 10.1063/1.4816465.
[24] B. T. Lejeune, X. Du, R. Barua, J. C. Zhao, and L. H. Lewis, “Anisotropic thermal conductivity of magnetocaloric AlFe2B2,” Materialia, vol. 1, no. May, pp. 150–154, 2018, doi: 10.1016/j.mtla.2018.05.011.
[25] A. Mostafaei, P. R. De Vecchis, E. L. Stevens, and M. Chmielus, “Sintering regimes and resulting microstructure and properties of binder jet 3D printed Ni-Mn-Ga magnetic shape memory alloys,” Acta Mater., vol. 154, pp. 355–364, 2018, doi: 10.1016/j.actamat.2018.05.047.
[26] X. Miao et al., “Printing (Mn,Fe)2(P,Si) magnetocaloric alloys for magnetic refrigeration applications,” J. Mater. Sci., vol. 55, no. 15, pp. 6660–6668, 2020, doi: 10.1007/s10853-020-04488-8.
[27] K. Navickaitė, J. Liang, C. R. H. Bahl, S. Wieland, T. Buchenau, and K. Engelbrecht, “Experimental characterization of active magnetic regenerators constructed using laser beam melting technique,” Appl. Therm. Eng., vol. 174, p. 115297, 2020, doi: 10.1016/j.applthermaleng.2020.115297.
[28] J. Tušek, K. Engelbrecht, D. Eriksen, S. Dall’Olio, J. Tušek, and N. Pryds, “A regenerative elastocaloric heat pump,” Nat. Energy, vol. 1, no. 10, 2016, doi: 10.1038/nenergy.2016.134.
[29] D. Catalini, N. Emaikwu, Y. Hwang, R. Radermacher, and I. Takeuchi, “Elastocaloric Cooling,” vol. 37, no. 3, pp. 29–32, 2019.
[30] P. Kabirifar, A. Žerovnik, Ž. Ahčin, L. Porenta, M. Brojan, and J. Tušek, “Elastocaloric Cooling: State-of-the-art and Future Challenges in Designing Regenerative Elastocaloric Devices,” Strojniški Vestn. – J. Mech. Eng., vol. 65, no. 11–12, pp. 615–630, Nov. 2019, doi: 10.5545/sv-jme.2019.6369.
[31] K. Engelbrecht et al., “Effects of surface finish and mechanical training on Ni-Ti sheets for elastocaloric cooling,” APL Mater., vol. 4, no. 6, p. 064110, Jun. 2016, doi: 10.1063/1.4955131.
[32] K. Navickaitė et al., “Plasma electrolytic polishing of Nitinol : Investigation of functional properties,” Materials (Basel)., vol. 14, p. 6450, 2021, doi: 10.3390/ma14216450.
[33] M. T. Andani, C. Haberland, J. Walker, and M. Elahinia, “An Investigation of Effective Process Parameters on Phase Transformation Temperature of Nitinol Manufactured by Selective Laser Melting,” in Proceedings of the ASME 2014 Conference on Smart Materials, Adaptive Structures and Intelligent Systems, Sep. 2014, pp. 1–5, doi: 10.1115/SMASIS2014-7649.
[34] H. Hou et al., “Elastocaloric cooling of additive manufactured shape memory alloys with large latent heat,” J. Phys. D. Appl. Phys., vol. 50, no. 40, 2017, doi: 10.1088/1361-6463/aa85bf.
[35] H. Hou et al., “Fatigue-resistant high-performance elastocaloric materials made by additive manufacturing,” Science (80-. )., vol. 366, no. 6469, pp. 1116–1121, 2019, doi: 10.1126/science.aax7616.
Image credit (for illustration purposes only): Oak Ridge National Laboratory. Polymer Additive Manufacturing lab at the Manufacturing Demonstration Facility. https://flic.kr/p/ePhuYa
Search in the encyclopedia for articles on the following topics:
Cryogenics and gas processing | Refrigerants and secondary refrigerants | Refrigerating equipment | Cryobiology and cryomedicine, freeze-drying | Application of refrigeration to perishable products | Refrigerated storage | Heat pumps, energy recovery | General information on refrigeration, energy and environment