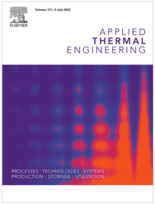
Development of an improved dynamic model of a Stirling engine and a performance analysis of a cogeneration plant.
Author(s) : CACABELOS A., EGUÍA P., MÍGUEZ J. L., et al.
Type of article: Article
Summary
In this paper, the authors develop a dynamic model of a commercial micro-combined heat and power (mCHP) unit and analyse its dynamic behaviour when the engine is running at different mass flow inputs. The simulation predicts with a low root mean bias error (RMSE) the most important outputs from the cogeneration unit during the starting, steady-state and stopping periods. Furthermore, the presented transient model reproduces the behaviour of the cogeneration unit when the fuel and air mass flows are changing. The obtained results are discussed, and the different possibilities for the variation of the thermal to power ratio are analysed. These combinations include the variation of the flow distribution inside the machine and the position of the exhaust heat exchanger. The power to thermal ratio can be modified between 0.15 and 0.26 for these combinations. The performance of the engine and the variation of the heat source temperature are also analysed theoretically. The simulation results conclude that an important saving could be obtained when the electrical to thermal ratio (ETTR) is tracked for the power or thermal demands from a dwelling.
Details
- Original title: Development of an improved dynamic model of a Stirling engine and a performance analysis of a cogeneration plant.
- Record ID : 30014829
- Languages: English
- Source: Applied Thermal Engineering - vol. 73 - n. 1
- Publication date: 2014/12
- DOI: http://dx.doi.org/10.1016/j.applthermaleng.2014.07.078
Links
See other articles in this issue (44)
See the source
Indexing
- Themes: Cogeneration (CHP), trigeneration
- Keywords: Stirling; Performance; Optimization; Modelling; Expérimentation; Cogeneration
-
Optimization of electricity make/buy decisions ...
- Author(s) : RAMARAJ S., BRAUN J. E., HORTON W. T.
- Date : 2016/07/11
- Languages : English
- Source: 2016 Purdue Conferences. 4th International High Performance Buildings Conference at Purdue.
- Formats : PDF
View record
-
Econometric and environmental optimization of c...
- Author(s) : RAMARAJ S., BRAUN J. E., HORTON W. T.
- Date : 2018/07/09
- Languages : English
- Source: 2018 Purdue Conferences. 5th International High Performance Buildings Conference at Purdue.
- Formats : PDF
View record
-
Polygeneration for an off-grid Indian village: ...
- Author(s) : RAY A., JANA K., DE S.
- Date : 2017/04
- Languages : English
- Source: Applied Thermal Engineering - vol. 116
View record
-
Analyse exergoéconomique des installations de t...
- Author(s) : PANAIT T., UZUNEANU K., DRAGAN M., et al.
- Date : 2008
- Languages : French
- Source: Ann. Univ. Dunarea Jos Galati, IV - vol. 12
View record
-
4E Analysis of a new cogeneration system coupli...
- Author(s) : SUN D., QIN J., LIU Z.
- Date : 2024/12
- Languages : English
- Source: International Journal of Refrigeration - Revue Internationale du Froid - vol. 168
- Formats : PDF
View record