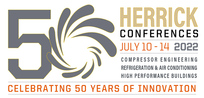
Development of experimental test rig for internally geared screw compressors.
Number: 1552
Author(s) : KRUPA A., KOVACEVIC A., READ M.
Summary
Gerotor pumps operate with two rotors, each rotating in the same direction about parallel but offset axes. Commerical applications for these machines include oil pumps, fuel pumps and hydraulic power transmission. It is also possible to use the gerotor configuration to achieve internal compression by specifying appropriate discharge port geometry, and the addition of helical twist to the rotors has been shown to achieve further benefits of reducing porting losses and power transfer between rotors. These internally-geared screw compressors have a number of potential advantages over conventional twin-screw configurations, including reduced leakage areas, co-directional thermal expansion, reduced rotor deflection, reduced viscous losses, and higher swept volume for a given machine envelope. Many of the loss mechanisms in these machines are similar in nature to conventional twin-screw machines but must be characterised due to the unique aspects of sealing line geometry and co-rotation (leading to much lower sliding velocities at contact points). Experimental testing is an essential step for model validation and appraisal of the potential benefits of this technology. This paper describes the test rig that is currently being developed to investigate the operation and performance of internally-geared machines, and how the how the geometry of a prototype machine has been specified.
Available documents
Format PDF
Pages: 10 p.
Available
Free
Details
- Original title: Development of experimental test rig for internally geared screw compressors.
- Record ID : 30030306
- Languages: English
- Subject: Technology
- Source: 2022 Purdue Conferences. 26th International Compressor Engineering Conference at Purdue.
- Publication date: 2022/07/15
Links
See other articles from the proceedings (83)
See the conference proceedings
Indexing
- Themes: Compressors
- Keywords: Test rig; Screw compressor; Expérimentation; Rotor; Design; Geometry; Modelling; Prototype
-
Development of a new engaging couple profile of...
- Author(s) : WU W., FENG Q., XU J., et al.
- Date : 2007/08/21
- Languages : English
- Source: ICR 2007. Refrigeration Creates the Future. Proceedings of the 22nd IIR International Congress of Refrigeration.
- Formats : PDF
View record
-
A new single screw compressor with profiles env...
- Author(s) : XU J., FENG Q., WU W.
- Date : 2007/08/21
- Languages : English
- Source: ICR 2007. Refrigeration Creates the Future. Proceedings of the 22nd IIR International Congress of Refrigeration.
- Formats : PDF
View record
-
Study on the performance of the boil-off gas tw...
- Author(s) : ZHOU Y., GUO Y., WANG Y., DIAO A., PENG X.
- Date : 2024/07
- Languages : English
- Source: International Journal of Refrigeration - Revue Internationale du Froid - vol. 163
- Formats : PDF
View record
-
The development of a new generation of open-typ...
- Author(s) : LIU Y., WU H., JIANG S., et al.
- Date : 2007/08/21
- Languages : English
- Source: ICR 2007. Refrigeration Creates the Future. Proceedings of the 22nd IIR International Congress of Refrigeration.
- Formats : PDF
View record
-
Basic design procedure for an internally geared...
- Author(s) : READ M.
- Date : 2021/09
- Languages : English
- Source: 12th International Conference on Compressors and their Systems
- Formats : PDF
View record