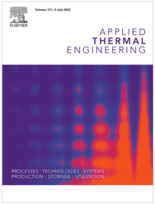
Investigation of transpiration cooling for sintered metal porous struts in supersonic flow.
Author(s) : HUANG Z., ZHU Y. H., XIONG Y. B., et al.
Type of article: Article
Summary
Struts are used to inject fuel into the combustor in some scramjet engines, where the flow within the combustor and nozzle is always supersonic. Tremendous aerodynamic heating causes challenging design issues concerning the thermal protection of the strut. This study investigates cooling of a sintered porous strut using transpiration cooling to protect the strut from ablation. Numerical simulations were used to study the transpiration cooling for different strut structures, material properties and coolant conditions. The influences of these parameters on the transpiration cooling of the strut were analyzed for a main stream Mach number of 2.5 and a total temperature of 1920 K. The results show that the surface average cooling effectiveness increasing extent decreases with the increasing coolant blowing ratio. Meanwhile, the retention time of mixture of main stream and injected coolant increases with the increasing coolant blowing ratio. The wedge angle of the strut has a significant influence on the cooling performance and the optimum strut wedge angle is near 30°. Increasing the strut material thermal conductivity also enhances the cooling effectiveness and reduces the thermal stresses.
Details
- Original title: Investigation of transpiration cooling for sintered metal porous struts in supersonic flow.
- Record ID : 30012291
- Languages: English
- Source: Applied Thermal Engineering - vol. 70 - n. 1
- Publication date: 2014/09
- DOI: http://dx.doi.org/10.1016/j.applthermaleng.2014.02.076
Links
See other articles in this issue (22)
See the source
Indexing
- Themes: Other industrial applications
- Keywords: Transpiration; Transport; Cooling; Engine; Model; Space
-
An experimental investigation on transpiration ...
- Author(s) : WANG J., ZHAO L., WANG X., et al.
- Date : 2014/08
- Languages : English
- Source: International Journal of Heat and Mass Transfer - vol. 75
View record
-
An experimental investigation on transpiration ...
- Author(s) : ZHAO L. J., WANG J. H., MA J., et al.
- Date : 2014/10
- Languages : English
- Source: International Journal of thermal Sciences - vol. 84
View record
-
Review of Advanced Effusive Cooling for Gas Tur...
- Author(s) : WANG W., YAN Y., ZHOU Y., CUI J.
- Date : 2022/11
- Languages : English
- Source: Energies - vol. 15 - n. 22
- Formats : PDF
View record
-
Numerical Investigation on the Mechanism of Tra...
- Author(s) : YANG H., LIU X., BIAN Y., WANG G.
- Date : 2022/03
- Languages : English
- Source: Energies - vol. 15 - n. 6
- Formats : PDF
View record
-
Experimental and numerical investigation of tra...
- Author(s) : LIU Y. Q., JIANG P. X., XIONG Y. B., et al.
- Date : 2013/01
- Languages : English
- Source: Applied Thermal Engineering - vol. 50 - n. 1
View record