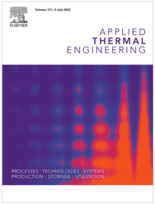
Containment capsule stresses for encapsulated phase change materials.
Author(s) : BLANEY J. J., NETI S., MISIOLEK W. Z., et al.
Type of article: Article
Summary
The encapsulation of a phase change material to store thermal energy is considered here for concentrated solar power systems. The stress distribution in a spherical nickel shell of 250 µ thickness formed around a ball of zinc by the electroless deposition process and a stainless steel cylindrical shell containing zinc are considered. The effect of external forces and imperfections within the shell structure that could affect the deformation are also modeled. The aim of the simulations performed is to establish a suitable thickness for the encapsulating material. It is concluded that while the shell can deform and safely withstand the anticipated expansion of the zinc, the added effects from point loads caused by the weight of the surrounding encapsulated capsules and other possible imperfections in the capsule structure could cause failure. A three-dimensional finite element model is used to establish the stresses in cylinders of different aspect ratio caused by the expansion of zinc as it melts inside of the encapsulation. The amount of void space that must be left inside of the capsule, so that the expansion of the zinc during phase change and the increase in gas pressure inside of the vessel will not cause failure of the shell, is determined from simulations. Results indicate that the cylinder with welded ends could easily contain up to 86% of the initial volume full of zinc with only a very small amount of plastic deformation, less than 0.5% strain, corresponding to an internal pressure of 2.03 MPa.
Details
- Original title: Containment capsule stresses for encapsulated phase change materials.
- Record ID : 30006083
- Languages: English
- Source: Applied Thermal Engineering - vol. 50 - n. 1
- Publication date: 2013/01
- DOI: http://dx.doi.org/10.1016/j.applthermaleng.2012.07.014
Links
See other articles in this issue (64)
See the source
-
Heat transfer analysis of encapsulated phase ch...
- Author(s) : ZHAO W., NETI S., OZTEKIN A.
- Date : 2013/01
- Languages : English
- Source: Applied Thermal Engineering - vol. 50 - n. 1
View record
-
Performance enhancement of ice storage capsules...
- Author(s) : WU L., YU J., YANG J., GAO W., ZHANG C., YU C.
- Date : 2024/02
- Languages : English
- Source: International Journal of Refrigeration - Revue Internationale du Froid - vol. 158
- Formats : PDF
View record
-
Formation of tetradecane nanoemulsion by low-en...
- Author(s) : SCHALBART P., KAWAJI M., FUMOTO K.
- Date : 2010/12
- Languages : English
- Source: International Journal of Refrigeration - Revue Internationale du Froid - vol. 33 - n. 8
- Formats : PDF
View record
-
Encapsulated phase change material under cyclic...
- Author(s) : KOUSKSOU T., BRUEL P.
- Date : 2010/12
- Languages : English
- Source: International Journal of Refrigeration - Revue Internationale du Froid - vol. 33 - n. 8
- Formats : PDF
View record
-
On the computational modelling of thermal energ...
- Author(s) : KATSOURINIS D., FOUNTI M., ROMERO-SÁNCHEZ M. D., et al.
- Date : 2010/09/01
- Languages : English
- Source: 9th Conference on Phase-Change Materials and Slurries for Refrigeration and Air Conditioning. Proceedings: Sofia, Bulgaria, September 29-October 1, 2010.
- Formats : PDF
View record