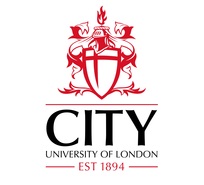
Research on motion and friction of rolling piston in rotary compressor.
Number: A3-140
Author(s) : XU J., YU B., DING S. P., ZHAO H. H.
Summary
Based on the Reynolds equation of mixed lubrication, the dynamic model of rolling piston was established, and the axis locus, rotation velocity, sliding velocity at vane tip, and friction loss of the piston were numerically solved. The analysis results indicated that the numeric results of sliding velocity at vane tip are in good agreement with the experimental results. In addition, the influences of crankshaft rotation speed, working condition, piston density and compression structure parameters on motion and friction were analyzed. Taking the ratio of piston rotation velocity and revolution velocity (λ) as evaluation index, whether λ conforms to cosine curve can judge the motion state between piston and vane. The results show that there is not only sliding state but also rolling state between piston and vane tip, and keeping rolling state is helpful to reduce friction loss. The design schemes of lighter piston, thicker vane and larger height-diameter ratio cylinder are proposed to keep rolling state in a wider rotation speed range and smaller pressure difference condition, thereby improving the annual operating efficiency of R32 rotary compressor.
Available documents
Format PDF
Pages: 10
Available
Free
Details
- Original title: Research on motion and friction of rolling piston in rotary compressor.
- Record ID : 30028740
- Languages: English
- Subject: Technology
- Source: 12th International Conference on Compressors and their Systems
- Publication date: 2021/09
- Document available for consultation in the library of the IIR headquarters only.
Links
See other articles from the proceedings (63)
See the conference proceedings
Indexing
- Themes: Compressors
- Keywords: Rotary compressor; Rolling piston compressor; Modelling; Calculation; Simulation; Friction; Reynolds; R32
-
USE OF A SIMULATION MODEL FOR THEORETICAL OPTIM...
- Author(s) : FRANCO DA COSTA C. M.
- Date : 1986/08/04
- Languages : English
View record
-
SUBSURFACE STRESSES IN ROLLING/SLIDING MACHINE ...
- Author(s) : SADEGHI F., SUI P. C.
- Date : 1988/07/18
- Languages : English
View record
-
THE HIGH MECHANICAL EFFICIENCY OF ROLLING-PISTO...
- Author(s) : ISHII N.
- Date : 1989/08/01
- Languages : English
View record
-
THE ANALYSIS OF DIMENSIONAL COMMONIZATION PROCE...
- Author(s) : COSTA C. F. DA
- Date : 1988/07/18
- Languages : English
View record
-
THE ESTIMATION OF THE FRICTIONAL LOSSES OF THE ...
- Author(s) : ZHOU Z., GONG Y.
- Date : 1988/07/18
- Languages : English
View record