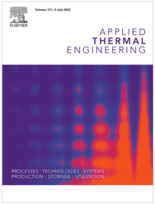
Simulation of exhaust gas heat recovery from a spray dryer.
Author(s) : GOLMAN B., JULKLANG W.
Type of article: Article
Summary
This study explored various alternatives in improving the energy utilization of spray drying process through the exhaust gas heat recovery. Extensible and user-friendly simulation code was written in Visual Basic for Applications within Microsoft Excel for this purpose. The effects of process parameters were analyzed on the energy efficiency and energy saving in the industrial-scale spray drying system with exhaust gas heat recovery in an air-to-air heat exchanger and in the system with partial recirculation of exhaust air. The spray dryer is equipped with an indirect heater for heating the drying air. The maximum gains of 16% in energy efficiency and 50% in energy saving were obtained for spray drying system equipped with heat exchanger for exhaust air heat recovery. In addition, 34% in energy efficiency and 61% in energy saving for system with recirculation of exhaust air in the present range of process parameters. The high energy efficiency was obtained during drying of large amount of dilute slurry. The energy saving was increased using the large amount of hot drying air.
Details
- Original title: Simulation of exhaust gas heat recovery from a spray dryer.
- Record ID : 30014893
- Languages: English
- Source: Applied Thermal Engineering - vol. 73 - n. 1
- Publication date: 2014/12
- DOI: http://dx.doi.org/10.1016/j.applthermaleng.2014.08.045
Links
See other articles in this issue (44)
See the source
Indexing
- Themes: Other energy-saving and energy-recovery systems
- Keywords: Spray; Exhaust air; Heat recovery; Simulation; Drying; Energy efficiency; Energy saving
-
Experimental tests on different systems for hea...
- Author(s) : SERRAINO M., RANZATO G.
- Date : 2007/06/08
- Languages : English
- Source: Technological innovations in air-conditioning and refrigeration industry + CD-ROM.
View record
-
Determining the air exchange efficiency of supp...
- Date : 1997/06
- Languages : German
- Source: Gesund. Ing. - vol. 118 - n. 3
View record
-
Installations de récupération de chaleur : un c...
- Author(s) : SAX M., CAENEGEM L. van, SCHICK M.
- Date : 2012/09
- Languages : French
- Source: Recherche agronomique Suisse - n. 9
- Formats : PDF
View record
-
Heating/Cooling Fresh Air Using Hot/Cold Exhaus...
- Author(s) : KHALED M., ALI S., JABER H., FARAJ J., MURR R., LEMENAND T.
- Date : 2022/03
- Languages : English
- Source: Energies - vol. 15 - n. 5
- Formats : PDF
View record
-
Minnesota school combines indoor-air quality ne...
- Date : 1996/04/15
- Languages : English
- Source: Air Cond. Heat. Refrig. News - vol. 70
View record