Additive manufacturing of heat exchangers
In the refrigeration industry, additive manufacturing (colloquially referred to as “3D printing”) makes it possible to fabricate novel, complex and potentially more energy efficient heat exchanger geometries than traditional manufacturing methods. Such heat exchangers could be used to enhance the thermohydraulic efficiency of heat pumps and cooling devices as well as to improve the cooling efficiency of electronic devices.
What is additive manufacturing and 3D printing?
The term “additive manufacturing” (AM) refers to a class of technologies based on layer-by-layer fabrication using 3D model data. [2,3] Contrary to conventional manufacturing processes, such as cutting and milling, in which material is subtracted from a bulk piece, materials in AM processes are added layer-by-layer to form the desired object. Simply put, to create an object using AM, one must first create a design, typically using a computer-aided design (CAD) software or by scanning the object. The software then translates the design into a framework for the additive manufacturing machine to follow. [4]
The term “3D printing” is often used in colloquial language in place of “additive manufacturing”, even though the latter is a broader term that encompasses a wider range of processes. According to the ISO/ASTM standard, the term “additive manufacturing” is most commonly associated with industrial applications, whereas the term “3D printing” is typically associated with machines used for non-industrial purposes including personal use (e.g. domestic or semi-professional equipment). [2,5]
AM allows to fabricate a wide range of structures and complex geometries. Initially developed in 1986 for processing polymers, waxes and paper laminates for prototyping purposes, AM has evolved over the years and now involves various methods, materials and equipment. [6]
Geometry and efficiency of additively manufactured heat exchangers
Various studies agree that AM makes it possible to fabricate novel, complex and potentially more energy efficient heat exchanger geometries than traditional manufacturing methods. Complex internal geometries can be fabricated in one step, in a material-efficient way and with lower volume. [7] Provided the geometry is suitably optimised, additively manufactured heat exchangers can meet the requirements for an effective heat exchanger. For instance, the pressure-drop across an additively manufactured heat exchanger can be reduced, and the surface-to-volume ratio can be increased, therefore allowing the energy density of the heat exchanger to be enhanced. [8] Furthermore, the single-step printing process of AM produces jointless components, which lowers the risk of leakage. [9]
The volume of research using AM to create new cutting-edge heat exchangers and heat sinks has rapidly increased over the past few years. Consequently, different types of materials are used to additively manufacture heat exchangers, e.g., polymers, metals and ceramics.
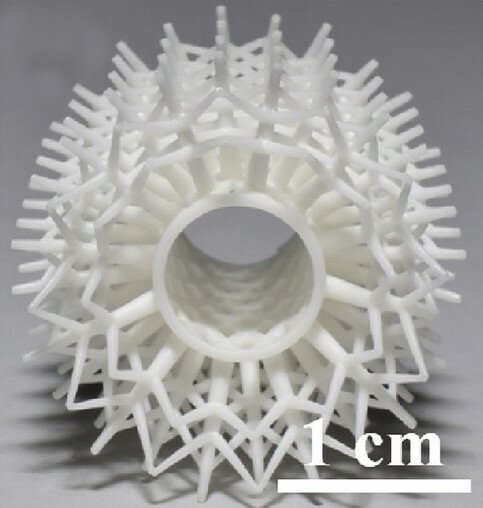
Performance of additively manufactured polymer heat exchangers
Polymers have historically been used for AM for longer than any other materials and their processing has therefore been more thoroughly investigated. Polymers offer the benefits of low weight, low manufacturing cost, anticorrosion, and electrical insulation. One study presented an air-to-water heat exchanger additively manufactured using Laser Polymer Welding (LPW). Compared with a metal heat exchanger with wavy fins of the same capacity, the mass of the polymer heat exchanger was reduced by 85% but the volume increased by 35%. The coefficient of performance (COP) achieved with the polymer heat exchanger was 27% higher than that of the metal heat exchanger. [10]
However, polymers typically have lower thermal conductivity than metals. Researchers have pursued two approaches to improve the thermal conductivity of additively manufactured polymer heat exchangers. One approach involves novel designs with reduced wall thickness (~100 µm) to compensate for the low thermal conductivity. The other approach involves the development of polymer composite materials with higher thermal conductivities than conventional polymers. This is achieved by filling the polymer matrix with thermally conductive materials such as metallic, carbon-based, and ceramic fillers. [11]
In a study on dry cooling applications, researchers fabricated a novel composite polymer heat exchanger (CMHX) and compared its performance to respective state-of-the-art heat exchangers. The fabricated CMHX was an air-water heat exchanger consisting of continuous high conductivity metal wires which directly pass through the polymer tube walls. The AM technique used was a patent-pending, fused filament fabrication 3D printer head. Compared to the conventional heat exchangers, the CMHX displayed up to 220% and 125% increase heat flow rate over mass (Q/m) and heat flow rate over volume (Q/V), respectively, for the same COP. The corresponding effective thermal conductivity of the CMHX was 130 W/(m K), which is several times higher than that of the state-of-the-art polymer or polymer composite heat exchangers. Moreover, as the CMHX was additively manufactured using commercially available metal wires, the researchers estimated that mass production costs would be lower. [11]
Performance of additively manufactured metal heat exchangers
With traditional manufacturing methods, metals are commonly used to create heat exchangers due to their high thermal conductivity. With AM, high energy input is required to fabricate metal heat exchangers due to the high melting temperatures of metals (starting at around 660°C for aluminium and going up to 1670°C for titanium, which are some of the most common metals and alloys used in AM).
Nevertheless, high quality metal heat exchangers can be fabricated using AM. For example, owing to the excellent thermal conductivity of copper, several studies have considered using AM to produce copper heat exchangers with complex geometries and internal cooling channels. [3,8] Furthermore, several experimental studies have tested prototypes that offered mass or volume reductions when compared with commercially available metal heat exchangers. [7]
In one study, a compact PCM-based thermal battery with additively manufactured metal surfaces was proposed for thermal energy storage and recovery in 5G electronics. Organic paraffin and fatty acid PCMs were embedded within aluminium silicon alloy (AlSi10Mg) grid heat exchangers. Three different grid designs were investigated and compared with a simple planar heat exchanger without grid extension (see figures 1 and 2). All heat exchangers were additively manufactured from aluminium silicon alloy (AlSi10Mg) using Selective Laser Melting (SLM). The laboratory scale experiments revealed that the additively manufactured grid surfaces of GHE significantly reduced the charging and discharging time from more than 240 min to less than 20 min. In contrast to the planar heat exchanger, the grid heat exchanger may increase thermal power by a factor of about 20 from 35 W to 670 W. [12]
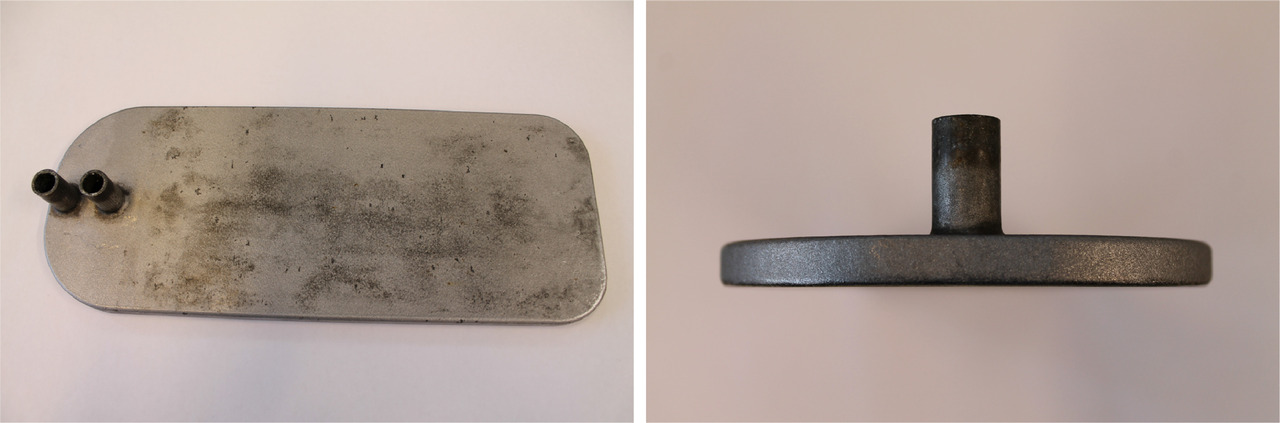
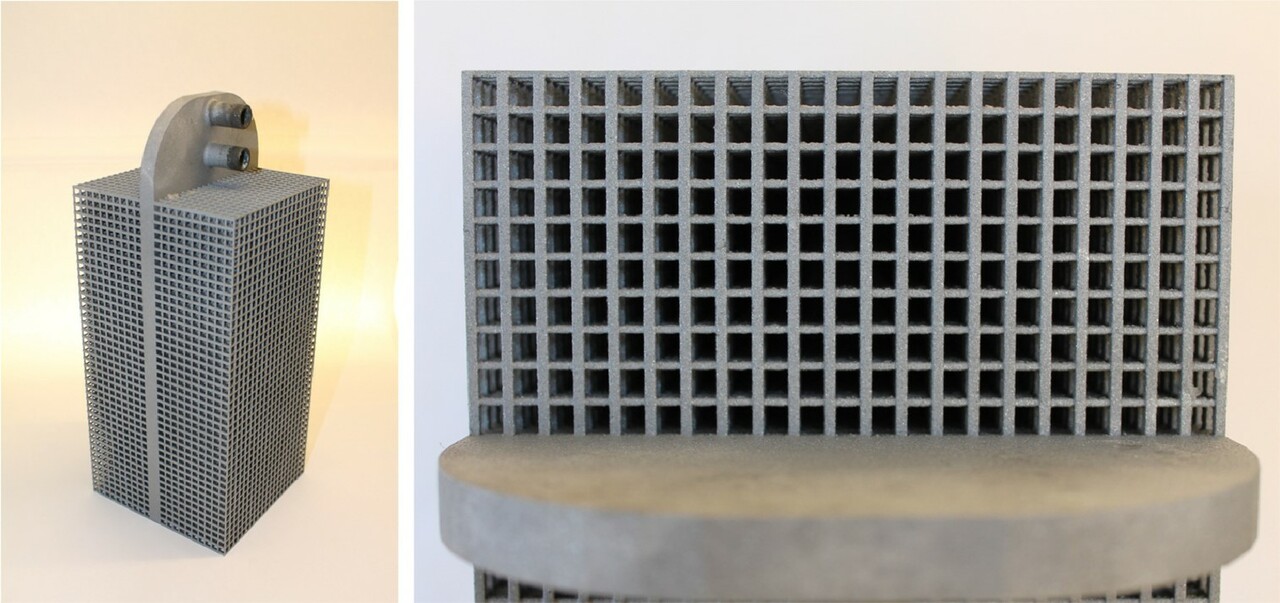
Performance of additively manufactured ceramic heat exchangers
Ceramic heat exchangers have gained increasing attention mainly for high temperature applications. [3] Indeed, ceramics possess excellent reliability regarding high temperatures, abrasion and extreme chemical environments. [7] In recent years, complex porous structures (such as lattices) have been investigated to improve the performance of high temperature heat exchangers. Ceramic lattices, often made of alumina (Al2O3), zirconia (ZrO2) or silicon carbide (SiC), are widely used as they withstand both high temperature and oxidation. The design of such complex structures depends as much on the manufacturing technique used as on purpose-built algorithms or software that can generate lattice structures with several parametric variables. [13]
A team of researchers used additive manufacturing to develop silicon carbide (SiC) ceramic lattices for a high temperature gas-to-gas heat exchanger designed for a project using concentrated solar thermal power to produce hydrogen. The lattice architecture was designed to provide the best compromise between effective thermal conductivity, specific surface area, dispersion coefficient and pressure loss, compared to other geometries. CFD simulations were used to determine the heat transfer behaviour of various lattice configurations. [13]
|
|
In another study, tubular heat exchangers were fabricated out of alumina comprising lattice structure of three different cellular structures. The authors applied the stereolithography technique to fabricate the lattices and achieved an optimised heat transfer of 160% to 280% between cold flowing air and the ceramic tube. [3]
Challenges of additive manufacturing of refrigeration components
AM offers the possibility for increased geometrical complexity and allows the fabrication of novel heat exchanger designs. However, design complexity does not guarantee improved heat transfer. Therefore, evaluating the thermal performance of these novel heat exchangers is a challenge, especially for particularly complex designs. [3,14]
Moreover, minor imperfections may occur during the AM process which can affect the thermal or mechanical properties of the manufactured part. [15] For example, due to pore formation caused by successive layers in additive manufacturing, unwanted microporosity occurs.
Furthermore, since metals and their alloys are usually additively manufactured by heat fusion, the addition of subsequent layers reheats the boundaries of the previous layers resulting in differences in the microstructure of the material inside each layer. Consequently, the microporosity and differences in the microstructure cause anisotropic thermal conductivity and mechanical properties of the manufactured parts. [14,16] Anisotropic behaviour results in a different mechanical behaviour of the additively manufactured part under vertical tension or compression compared to that in the horizontal direction.[16] The microporosity of the AM parts can be minimised by adjusting the process parameters, such as laser power, scan speed, etc.[17]
Post-processing of additive manufactured parts in order to remove imperfections, such as partly melted particles, is more challenging than for traditionally manufactured parts. [7] Nevertheless, novel polishing techniques are being developed, suitable for additive manufactured complex geometries. [15,18]
Useful links for further information
-
Open access articles
Sarap, M.; Kallaste, A.; Shams Ghahfarokhi, P.; Tiismus, H.; Vaimann, T. Utilization of Additive Manufacturing in the Thermal Design of Electrical Machines: A Review. Machines 2022, 10, 251. https://doi.org/10.3390/machines10040251
Ralls, A.M.; Kumar, P.; Menezes, P.L. Tribological Properties of Additive Manufactured Materials for Energy Applications: A Review. Processes 2021, 9, 31. https://doi.org/10.3390/pr9010031
Jiang, Q.; Zhang, P.; Yu, Z.; Shi, H.; Wu, D.; Yan, H.; Ye, X.; Lu, Q.; Tian, Y. A Review on Additive Manufacturing of Pure Copper. Coatings 2021, 11, 740. https://doi.org/10.3390/coatings11060740
Stepputat, V.N.; Zeidler, H.; Safranchik, D.; Strokin, E.; Böttger-Hiller, F. Investigation of Post-Processing of Additively Manufactured Nitinol Smart Springs with Plasma-Electrolytic Polishing. Materials 2021, 14, 4093. https://doi.org/10.3390/ma14154093
Jiménez, M., Romero, L., Domínguez, I. A., Espinosa, M. del M., & Domínguez, M. (2019). Additive Manufacturing Technologies: An Overview about 3D Printing Methods and Future Prospects. Complexity, 2019, e9656938. https://doi.org/10.1155/2019/9656938
And also, for further information on heat exchangers, the following documents are available for download on FRIDOC.
-
Guide/Handbook
2016 ASHRAE Handbook. HVAC systems and equipment (SI edition). Chapter 48- Heat exchangers. https://iifiir.org/en/fridoc/2016-ashrae-handbook-hvac-systems-and-equipment-si-edition-4721 -
Conference paper
Klein, E., Ling, J., Aute, V., Hwang, Y., & Radermacher, R. (2018, January). A Review of Recent Advances in Additively Manufactured Heat Exchangers. 17th International Refrigeration and Air Conditioning Conference. https://iifiir.org/en/fridoc/34106
6th IIR Conference on Thermophysical Properties and Transfer Processes of Refrigerants https://iifiir.org/en/fridoc/6-lt-sup-gt-th-lt-sup-gt-iir-conference-on-thermophysical-properties-and-144168
Acknowledgements
The IIR would like to thank Dr Kristina NAVICKAITE, junior member of the E1 commission “Air conditioning”, for co-authoring this summary document.
References
1. Chen, Z., Li, Z., Li, J., Liu, C., Lao, C., Fu, Y., Liu, C., Li, Y., Wang, P., & He, Y. (2019). 3D printing of ceramics: A review. Journal of the European Ceramic Society, 39(4), 661–687. https://doi.org/10.1016/j.jeurceramsoc.2018.11.013
2. ISO/ASTM. (2021). ISO/ASTM 52900:2021. Additive manufacturing—General principles—Fundamentals and vocabulary. https://www.iso.org/obp/ui/#iso:std:iso-astm:52900:ed-2:v1:en
3. Niknam, S. A., Mortazavi, M., & Li, D. (2021). Additively manufactured heat exchangers: A review on opportunities and challenges. The International Journal of Advanced Manufacturing Technology, 112(3), 601–618. https://doi.org/10.1007/s00170-020-06372-w
4. Linke, R. (2017, December 7). Additive manufacturing, explained. MIT Sloan School of Management. https://mitsloan.mit.edu/ideas-made-to-matter/additive-manufacturing-explained
5. Jiménez, M., Romero, L., Domínguez, I. A., Espinosa, M. del M., & Domínguez, M. (2019). Additive Manufacturing Technologies: An Overview about 3D Printing Methods and Future Prospects. Complexity, 2019, e9656938. https://doi.org/10.1155/2019/9656938
6. Loughborough University. (n.d.). The 7 categories of Additive Manufacturing. Additive Manufacturing Research Group. Additive Manufacturing Research Group. Retrieved 15 February 2022, from https://www.lboro.ac.uk/research/amrg/about/the7categoriesofadditivemanufacturing/
7. Klein, E., Ling, J., Aute, V., Hwang, Y., & Radermacher, R. (2018, January 1). A Review of Recent Advances in Additively Manufactured Heat Exchangers. 17th International Refrigeration and Air Conditioning Conference. https://iifiir.org/en/fridoc/34106
8. Laitinen, V., Merabtene, M., Stevens, E., Chmielus, M., Van Humbeeck, J., & Ullakko, K. (2020). Additive Manufacturing from the Point of View of Materials Research. In M. Collan & K.-E. Michelsen (Eds.), Technical, Economic and Societal Effects of Manufacturing 4.0: Automation, Adaption and Manufacturing in Finland and Beyond (pp. 43–83). Springer International Publishing. https://doi.org/10.1007/978-3-030-46103-4_3
9. Tran, T. Q., Chinnappan, A., Lee, J. K. Y., Loc, N. H., Tran, L. T., Wang, G., Kumar, V. V., Jayathilaka, W. a. D. M., Ji, D., Doddamani, M., & Ramakrishna, S. (2019). 3D Printing of Highly Pure Copper. Metals, 9(7), 756. https://doi.org/10.3390/met9070756
10. Deisenroth, D. C., Moradi, R., Shooshtari, A. H., Singer, F., Bar-Cohen, A., & Ohadi, M. (2018). Review of Heat Exchangers Enabled by Polymer and Polymer Composite Additive Manufacturing. Heat Transfer Engineering, 39(19), 1648–1664. https://doi.org/10.1080/01457632.2017.1384280
11. Arie, M. A., Hymas, D. M., Singer, F., Shooshtari, A. H., & Ohadi, M. (2020). An additively manufactured novel polymer composite heat exchanger for dry cooling applications. International Journal of Heat and Mass Transfer, 147, 118889. https://doi.org/10.1016/j.ijheatmasstransfer.2019.118889
12. Yazdani, M. R., Laitinen, A., Helaakoski, V., Farnas, L. K., Kukko, K., Saari, K., & Vuorinen, V. (2021). Efficient storage and recovery of waste heat by phase change material embedded within additively manufactured grid heat exchangers. International Journal of Heat and Mass Transfer, 181, 121846. https://doi.org/10.1016/j.ijheatmasstransfer.2021.121846
13. Pelanconi, M., Zavattoni, S., Cornolti, L., Puragliesi, R., Arrivabeni, E., Ferrari, L., Gianella, S., Barbato, M., & Ortona, A. (2021). Application of Ceramic Lattice Structures to Design Compact, High Temperature Heat Exchangers: Material and Architecture Selection. Materials, 14(12), 3225. https://doi.org/10.3390/ma14123225
14. Alsulami, M., Mortazavi, M., Niknam, S. A., & Li, D. (2020). Design complexity and performance analysis in additively manufactured heat exchangers. The International Journal of Advanced Manufacturing Technology, 110(3), 865–873. https://doi.org/10.1007/s00170-020-05898-3
15. Peng, X., Kong, L., Fuh, J. Y. H., & Wang, H. (2021). A Review of Post-Processing Technologies in Additive Manufacturing. Journal of Manufacturing and Materials Processing, 5(2), 38. https://doi.org/10.3390/jmmp5020038
16. Ngo, T. D., Kashani, A., Imbalzano, G., Nguyen, K. T. Q., & Hui, D. (2018). Additive manufacturing (3D printing): A review of materials, methods, applications and challenges. Composites Part B: Engineering, 143, 172–196. https://doi.org/10.1016/j.compositesb.2018.02.012
17. Martínez-Maradiaga, D., Mishin, O. V., & Engelbrecht, K. (2020). Thermal Properties of Selectively Laser-Melted AlSi10Mg Products with Different Densities. Journal of Materials Engineering and Performance, 29(11), 7125–7130. https://doi.org/10.1007/s11665-020-05192-z
18. Stepputat, V. N., Zeidler, H., Safranchik, D., Strokin, E., & Böttger-Hiller, F. (2021). Investigation of Post-Processing of Additively Manufactured Nitinol Smart Springs with Plasma-Electrolytic Polishing. Materials, 14(15), 4093. https://doi.org/10.3390/ma14154093
Illustrative figure. Pipe-shaped heat exchanger with complex 3D structures (adapted from [1] )
Search in the encyclopedia for articles on the following topics:
Cryogenics and gas processing | Refrigerants and secondary refrigerants | Refrigerating equipment | Cryobiology and cryomedicine, freeze-drying | Application of refrigeration to perishable products | Refrigerated storage | Heat pumps, energy recovery | General information on refrigeration, energy and environment