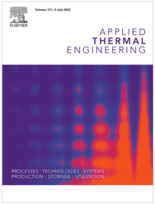
Summary
An ejector was used in a compression refrigeration cycle for improving its efficiency. A constant pressure mixing model was adopted to simulate the ejector. Whether or not the entrained flow would be choked at the outlet of the suction nozzle and whether or not a condensation shock would happen at the end of the mixing chamber were both considered. The effect of the mixing pressure on the performances of the ejector and the hybrid system was evaluated. The mixing pressure was finally determined by using the optimization method. The performances of the ejector and the hybrid system at different operating conditions were studied. Lastly, the performances of the ejector with fixed geometry and the corresponding hybrid system at off-design operating conditions were also theoretically studied. The results indicate that the optimum ejector mixing pressure is a little lower than the entrained fluid’s pressure, but far larger than its critical pressure. No condensation shock happens before it flows into the diffuser. The theoretical performances of the hybrid compression refrigeration system with fixed geometry ejector at off-design conditions are very close to that with the optimum geometry ejector.
Details
- Original title: Analysis for the ejector used as expansion valve in vapor compression refrigeration cycle.
- Record ID : 30016757
- Languages: English
- Source: Applied Thermal Engineering - vol. 96
- Publication date: 2016/03/05
- DOI: http://dx.doi.org/10.1016/j.applthermaleng.2015.11.095
Links
See other articles in this issue (32)
See the source
-
Design considerations for a second-generation C...
- Author(s) : NICKL J., WILL G., KRAUS W. E., et al.
- Date : 2002/09/17
- Languages : English
- Formats : PDF
View record
-
Water cooling by an expanding air stream.
- Author(s) : MAIYA M. P.
- Date : 1998/06/02
- Languages : English
- Source: Natural Refrigerants, Energy Efficiency, Cost and Safety. Natural Working Fluids '98. IIR-Gustav Lorentzen Conference.
- Formats : PDF
View record
-
Compressor and expansion machines for use in ai...
- Author(s) : SICARS S., ENGELKING S., KRUSE H.
- Date : 1993/11
- Languages : English
View record
-
Studies on the performance of a CO2 air conditi...
- Author(s) : LEE J. S., KIM M. S.
- Date : 2014/02
- Languages : English
- Source: International Journal of Refrigeration - Revue Internationale du Froid - vol. 38
- Formats : PDF
View record
-
Historical and present developments of ejector ...
- Author(s) : ELBEL S.
- Date : 2011/11
- Languages : English
- Source: International Journal of Refrigeration - Revue Internationale du Froid - vol. 34 - n. 7
- Formats : PDF
View record