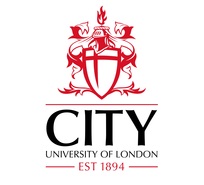
Experimental analysis of reed valve movement for different reed valve designs tested in an impact fatigue test system.
Number: C1-181
Author(s) : TOFIQUE M. W., LOF A., MILLWARD C.
Summary
Impact fatigue is a phenomenon that is the main cause of failure of reed valves in compressor systems. This phenomenon occurs in compressors due to repeated opening and closing of reed valves during suction and exhaust cycles of compressors. When the valve opens it creates bending fatigue stresses in the body of reed valve; when the valve closes it strikes against the valve plate creating impact stresses. This reed valve movement and impact is repeated billions of times. This cyclic movement influences the impact fatigue life of the reed valve and, hence, the performance of a compressor. The valve movement can be defined in terms of valve frequency, valve lift, valve velocity and impact velocity. Inside a reciprocating compressor, a number of parameters including the valve design, valve material, compressor operating frequency and suction/exhaust pressure influence the reed valve movement.
In this paper, we studied the valve movement parameters for three different suction reed valve designs manufactured from Flap-X – a martensitic stainless steel grade developed for reed valves – tested in a custom-built impact fatigue test system. The valves were excited into movement using compressed air pulses varying in frequency up to 300 Hz and varying pulse width. The valve displacement and frequency was recorded by a laser sensor at 10 000 frames per second. Before starting each test, the operating conditions such as the operating frequency and the air pulse width were pre-set in the impact fatigue test system’s control software while the applied pressure was kept constant during the test. The valve response was measured to be different for the different valve designs tested in this study. The reed valve design influenced the important reed movement parameters such as the valve lift, valve velocity, impact velocity and the frequency of valve vibrations. The valves were not tested to failure as the focus of this study was to collect the dynamic data of valve movement. However, for a practical impact fatigue testing of the reed valves intended to achieve fracture of valves, the testing should be conducted at higher frequencies to reduce test times as well as for a stable amplitude of vibration and impact velocity as shown in this study. The information obtained from this study shows the applicability of the presented impact fatigue test system to study the reed valve movement as well as their impact fatigue characteristics.
Available documents
Format PDF
Pages: 12
Available
Free
Details
- Original title: Experimental analysis of reed valve movement for different reed valve designs tested in an impact fatigue test system.
- Record ID : 30028766
- Languages: English
- Subject: Technology
- Source: 12th International Conference on Compressors and their Systems
- Publication date: 2021/09
- Document available for consultation in the library of the IIR headquarters only.
Links
See other articles from the proceedings (63)
See the conference proceedings
Indexing
- Themes: Compressors
- Keywords: Expérimentation; Valve (compressor); Fatigue; Reciprocating compressor; Frequency; Test rig
-
Experimental and numerical analysis of reed val...
- Author(s) : TOFIQUE M. W., LOF A., SCHILLACI E., CASTRILLO P., RIGOLA J.
- Date : 2021/05
- Languages : English
- Source: 2021 Purdue Conferences. 25th International Compressor Engineering Conference at Purdue.
- Formats : PDF
View record
-
Investigation of the influence of valve reed-im...
- Author(s) : TOFIQUE M. W., LOF A., MILLWARD C., et al.
- Date : 2018/07/09
- Languages : English
- Source: 2018 Purdue Conferences. 24th International Compressor Engineering Conference at Purdue.
- Formats : PDF
View record
-
Impact fatigue characteristics of valve leaves ...
- Author(s) : ALTUNLU A., LAZOGLU I., OGUZ E., et al.
- Date : 2010/07/12
- Languages : English
- Source: 2010 Purdue Conferences. 20th International Compressor Engineering Conference at Purdue.
- Formats : PDF
View record
-
AN EXPERIMENTAL TEST DEVICE FOR ACCELERATED END...
- Author(s) : HARTSHORN K.
- Date : 1986/08/04
- Languages : English
View record
-
A feature extraction method based on LMD and it...
- Author(s) : SHU Y., ZHANG Q., XIE C., et al.
- Date : 2018/07/09
- Languages : English
- Source: 2018 Purdue Conferences. 24th International Compressor Engineering Conference at Purdue.
- Formats : PDF
View record