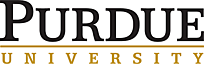
Experimental and numerical analysis of reed valve movement in an impact fatigue test system and reciprocating compressors.
Number: 1613
Author(s) : TOFIQUE M. W., LOF A., SCHILLACI E., CASTRILLO P., RIGOLA J.
Summary
During operation of a reciprocating compressor, its flapper valve opens to allow the passage of gases and closes by striking against the valve impact plate. This reed valve movement and impact is repeated billions of times. This cyclic movement has a significant influence on the impact fatigue life of the reed valve and, hence, the lifetime of a compressor. Inside a reciprocating compressor, a number of parameters including: the valve design, valve material, compressor operating frequency and suction/exhaust pressure, influence the reed valve movement. The valve movement can be defined in terms of valve frequency, valve lift, valve velocity and impact velocity. These response parameters heavily influence the compressor efficiency and impact fatigue life of reed valves. In this paper, we first studied the valve movement parameters for a reed valve design using an experimental test setup. In experimental testing, the valves were excited into movement using air pressure pulses at 100 Hz frequency (air pulse width of 5 milliseconds). The valve movement was recorded by a laser sensor at 10 000 frames per second. The operating conditions such as the operating frequency, air pulse width, applied pressure and airflow rate were measured. The valves were not tested to failure but only to collect the dynamic data of valve movement such as the valve movement curve (valve displacement vs time), average valve lift and reed velocity data. The experimental results were employed to validate a complex in-house 3D CFD finite-volume model aimed at studying in detail the valve and gas dynamics, whose interaction is solved by means of a Fluid-Structure Interaction (FSI) algorithm. The complete valve movement curve obtained from simulations – reed valve displacement vs time – correlated with that obtained from the experimental tests with small error. Similarly, the difference in experimental and numerically obtained average valve lift and impact velocity values were quite small for practical purposes. Finally, fluid-dynamic results for pressure and impact forces were employed to feed a finite-element based code aimed at studying the structural behavior of the reed vale. Bending fatigue and impact fatigue stresses induced in the reed valve during its movement cycle were calculated. The magnitude of stresses and their positioning was determined, which correlated with the commonly observed areas of fracture initiation in these valves.The numerical models, as well as the information obtained from this study will help the compressor manufacturers to design their compressors to enhance efficiency and reed valve’s reliability. This type of information is not readily available from a working compressor.
Available documents
Format PDF
Pages: 11
Available
Public price
20 €
Member price*
15 €
* Best rate depending on membership category (see the detailed benefits of individual and corporate memberships).
Details
- Original title: Experimental and numerical analysis of reed valve movement in an impact fatigue test system and reciprocating compressors.
- Record ID : 30028397
- Languages: English
- Subject: Technology
- Source: 2021 Purdue Conferences. 25th International Compressor Engineering Conference at Purdue.
- Publication date: 2021/05
- Document available for consultation in the library of the IIR headquarters only.
Links
See other articles from the proceedings (62)
See the conference proceedings
Indexing
- Themes: Compressors
- Keywords: Reciprocating compressor; CFD; Expérimentation; Test rig; Fatigue; Simulation; Valve (compressor)
-
Experimental analysis of reed valve movement fo...
- Author(s) : TOFIQUE M. W., LOF A., MILLWARD C.
- Date : 2021/09
- Languages : English
- Source: 12th International Conference on Compressors and their Systems
- Formats : PDF
View record
-
Investigation of the influence of valve reed-im...
- Author(s) : TOFIQUE M. W., LOF A., MILLWARD C., et al.
- Date : 2018/07/09
- Languages : English
- Source: 2018 Purdue Conferences. 24th International Compressor Engineering Conference at Purdue.
- Formats : PDF
View record
-
Coupled fluid-solid modelling of the valve dyna...
- Author(s) : ERVIK A., SAAI A., BERSTAD T., MEYER O., TSUJI T., OKU T., HATTORI K., YAMADA K., DELHAYE V., NEKSÅ P.
- Date : 2022/06/13
- Languages : English
- Source: 15th IIR-Gustav Lorentzen Conference on Natural Refrigerants (GL2022). Proceedings. Trondheim, Norway, June 13-15th 2022.
- Formats : PDF
View record
-
Experimental and numerical analysis of two diff...
- Author(s) : PASHAK P., SHAHZAD A., ABDULHAMID F., LAZOGLU I.
- Date : 2023/12
- Languages : English
- Source: International Journal of Refrigeration - Revue Internationale du Froid - Vol. 156
- Formats : PDF
View record
-
Impact fatigue characteristics of valve leaves ...
- Author(s) : ALTUNLU A., LAZOGLU I., OGUZ E., et al.
- Date : 2010/07/12
- Languages : English
- Source: 2010 Purdue Conferences. 20th International Compressor Engineering Conference at Purdue.
- Formats : PDF
View record