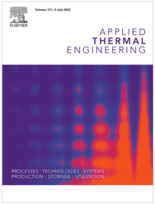
Summary
A vapor compression cycle, which is typically utilized for the heat pump, air conditioning and refrigeration systems, has inherent thermodynamic losses associated with expansion and compression processes. To minimize these losses and improve the energy efficiency of the vapor compression cycle, an ejector can be applied. However, due to the occurrence of complex physics i.e., non-equilibrium flashing compressible flow in the nozzle with possible shock interactions, it has not been feasible to model or optimize the design of a two-phase ejector. In this study, a homogeneous, non-equilibrium, two-phase flow computational fluid dynamics (CFD) model in a commercial code is used with an in-house empirical correlation for the mass transfer coefficient and real gas properties to perform a geometric optimization of a two-phase ejector. The model is first validated with experimental data of an ejector with R600a as the working fluid. After that, the design parameters of the ejector are optimized using multi-objective genetic algorithm (MOGA) based online approximation-assisted optimization (OAAO) approaches to find the maximum performance.
Details
- Original title: Optimization of two-phase R600a ejector geometries using a non-equilibrium CFD model.
- Record ID : 30019855
- Languages: English
- Source: Applied Thermal Engineering - vol. 109, part A
- Publication date: 2016/10/25
- DOI: http://dx.doi.org/10.1016/j.applthermaleng.2016.08.078
Links
See other articles in this issue (7)
See the source
Indexing
-
Themes:
Hydrocarbons;
Ejector systems, air cycle, Stirling cycle, other cycles) - Keywords: Two-phase flow; R600a; Geometry; CFD; Optimization; Modelling; Ejector
-
Analysis of application of two-phase injector i...
- Author(s) : SMIERCIEW K., BUTRYMOWICZ D., KWIDZINSKI R., et al.
- Date : 2015/03
- Languages : English
- Source: Applied Thermal Engineering - vol. 78
View record
-
CFD study of a variable area ratio ejector usin...
- Author(s) : VARGA S., LEBRE P. M. S., OLIVEIRA A. C.
- Date : 2013/01
- Languages : English
- Source: International Journal of Refrigeration - Revue Internationale du Froid - vol. 36 - n. 1
- Formats : PDF
View record
-
Experimental investigations of two-phase ejecto...
- Author(s) : SMIERCIEW K., GAGAN J., BUTRYMOWICZ D., et al.
- Date : 2019/08/24
- Languages : English
- Source: Proceedings of the 25th IIR International Congress of Refrigeration: Montréal , Canada, August 24-30, 2019.
- Formats : PDF
View record
-
A non symmetric interfacial area density formul...
- Author(s) : ORTEGO SAMPEDRO E.
- Date : 2021/05
- Languages : English
- Source: 2021 Purdue Conferences. 18th International Refrigeration and Air-Conditioning Conference at Purdue.
- Formats : PDF
View record
-
Shape optimisation of a two-phase ejector for C...
- Author(s) : PALACZ M., SMOLKA J., NOWAK A. J., et al.
- Date : 2017/02
- Languages : English
- Source: International Journal of Refrigeration - Revue Internationale du Froid - vol. 74
- Formats : PDF
View record