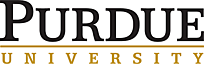
Recommended by the IIR
Miniature oil-less reciprocating compressor for high-lift, high-temperature heat pump applications.
Number: 1429
Author(s) : MURPHY D. L., KATANCIK M. S.
Summary
In the extreme temperature environment of the moon, the regolith surface temperature can reach 100°C during the 354-hour lunar day. This often exceeds the maximum allowable temperature of critical electronics onboard small lunar rovers designed for long-term science missions. In environments with such high heat sink temperatures, active vapor compression cooling solutions allow greater mission flexibility than traditional passive spacecraft thermal control. The objective of this research was to design and experimentally evaluate a critical enabling technology for effective lunar rover class heat pumps: the high-lift, high-temperature, microgravity compressor. The main technical challenges in the design of a compressor for these conditions include operation in a microgravity environment, relatively high compression ratio requirements, extreme temperatures during transport and operation in space and on the moon, and the low equipment vibration requirements for small lunar rovers. A twin-piston oil-less reciprocating compressor was designed to meet these requirements. The oil-less design mitigates the challenges of oil distribution in microgravity environments. A twin-piston configuration was designed to balance the dynamic forces and lower the vibration of the compressor. Compressor components were sized to operate with new high-temperature, environmentally friendly refrigerants at compression ratios between 3 and 7. The compressor was designed for a cooling capacity on the order of 100 W. A prototype compressor was fabricated and experimentally evaluated. The total mass of the compressor was 2.86 kg. Maximum exported vibration was estimated to be 0.04 N at the base of the compressor based on kinematic calculations and measured motor torque. Experimental capacity and efficiency measurements were lower than predicted. This was likely due to manufacturing and tolerance deficiencies in the first prototype compressor resulting in blowback around the piston seal, higher friction than predicted, suboptimal bearing performance, suboptimal reed valve design, and tolerance stack up in the crankshaft and cylinders. These manufacturing issues can be overcome in next generation prototypes.
Available documents
Format PDF
Pages: 10
Available
Public price
20 €
Member price*
15 €
* Best rate depending on membership category (see the detailed benefits of individual and corporate memberships).
Details
- Original title: Miniature oil-less reciprocating compressor for high-lift, high-temperature heat pump applications.
- Record ID : 30028381
- Languages: English
- Subject: Technology
- Source: 2021 Purdue Conferences. 25th International Compressor Engineering Conference at Purdue.
- Publication date: 2021/05
- Document available for consultation in the library of the IIR headquarters only.
Links
See other articles from the proceedings (62)
See the conference proceedings
Indexing
-
Industrial high temperature heat pump for steam...
- Author(s) : HAMACHER T.
- Date : 2023/05/15
- Languages : English
- Source: 14th IEA Heat Pump Conference 2023, Chicago, Illinois.
- Formats : PDF
View record
-
Experimental comparison of HCFO and HFO R1224yd...
- Author(s) : ARPAGAUS C., BERTSCH S. S.
- Date : 2021/05
- Languages : English
- Source: 2021 Purdue Conferences. 18th International Refrigeration and Air-Conditioning Conference at Purdue.
- Formats : PDF
View record
-
High temperature heat pump using HFO and HCFO r...
- Author(s) : ARPAGAUS C., KUSTER R., PRINZING M., et al.
- Date : 2019/08/24
- Languages : English
- Source: Proceedings of the 25th IIR International Congress of Refrigeration: Montréal , Canada, August 24-30, 2019.
- Formats : PDF
View record
-
Thermal dynamic analysis of low GWP alternative...
- Author(s) : YANG M., ZHANG H., QIN Y., NONG K.
- Date : 2023/04/05
- Languages : English
- Source: 3rd IIR conference on HFO Refrigerants and low GWP Blends. Shanghai, China.
- Formats : PDF
View record
-
Experimental results of a high-temperature heat...
- Author(s) : MOTA BABILONI A., BARRAGÁN-CERVERA A., UDROIU C-M., GIMÉNEZ-PRADES P., NAVARRO-ESBRÍ J.
- Date : 2023/08/21
- Languages : English
- Source: Proceedings of the 26th IIR International Congress of Refrigeration: Paris , France, August 21-25, 2023.
- Formats : PDF
View record