An award-winning industrial dairy using an integrated heat pump system
A recent case study examined the energy consumption and system performance of an innovative integrated heat pump system of a dairy located in Norway. This dairy was among the winning projects of the 2019 “Heat Pump City of the Year award” organised by the European Heat Pump Association (EHPA).
In recent years, the use of integrated high temperature heat pumps in combination with thermal storage tanks has been investigated as an efficient and environmentally friendly way to provide heating and cooling in industrial applications.
According to research, dairy plants are well suited for implementing high temperature heat pump systems. Indeed, processing of dairy products involves a combined application of product heating and cooling. In a conventional dairy, the heating demand is traditionally covered by fossil fuel boilers, while the cooling demand is covered by a separate refrigeration system. The need for fossil fuel could be eliminated by integrating an industrial heat pump that can deliver both process cooling and heating.
A recent case study investigated the energy consumption and system performance of the fully integrated heat pump system of a new dairy in Bergen, Norway. [1] This dairy was awarded the 2019 “Heat Pump City of the Year award” in the DecarbIndustry category, by the European Heat Pump Association. [2] To the authors’ best knowledge, this Norwegian dairy is the first in the world to operate without fossil fuel or direct electric heating.
Integrated heat pump system description
6000 m2 of photovoltaic solar panels are installed on the roof of the dairy, generating approximately 0.5 GWh of electricity annually. Ammonia chillers provide building and storage cooling. The dairy uses the excess heat from cooling processes to generate usable process heat at different temperature levels of 40 °C, 67 °C and 95 °C. The figure below illustrates the integrated heating and cooling system of the dairy, including three different heat pump systems and six temperature levels provided for the different production processes (pasteurizers, filling area and milk intake).
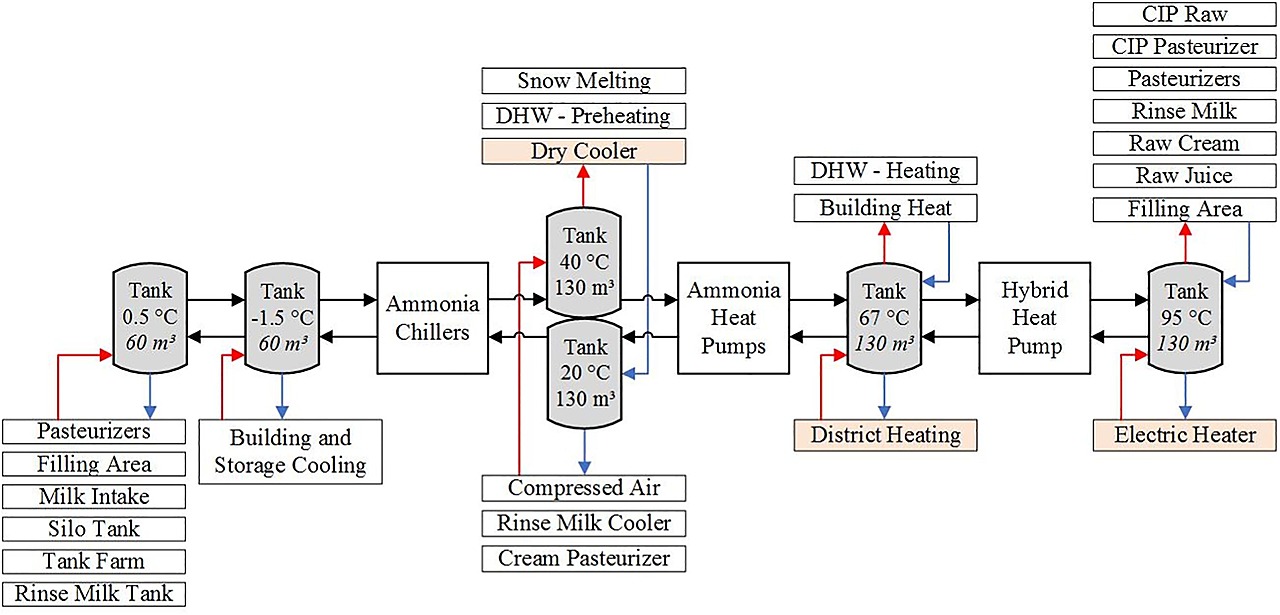
The heat pump systems are designed to provide nearly all required cooling and heating demands at the dairy, with the dry cooler, electric heater and district heating as backup resources. Table 1 presents a detailed overview of the installed heat pump systems.
Table 1. Overview of installed heat pump systems. [1]
System | Refrigerant |
Number of units |
Heat source |
Sink temperature |
Total capacity |
---|---|---|---|---|---|
Chillers |
NH3 | 3 |
4 °C / −1.5 °C |
20 °C / 40 °C |
2400 kW (cooling) |
Ammonia heat pumps |
NH3 | 2 |
40 °C / 20 °C |
60 °C / 67 °C |
1577 kW (heating) |
Hybrid absorption/compression heat pump |
NH3-H2O |
1 |
67 °C / 60 °C |
73 °C / 95 °C |
940 kW (heating) |
Integrated heat pump system performance
The authors evaluated the system performance using available operation data for a week between February 10th and February 17th 2020. In order to meet the demand for building and storage cooling, the chillers were in continuous operation throughout the week. Table 2 presents the performance data obtained for each element of the integrated system. The overall performance value achieved by the integrated system was a COP of 4.1 over a week.
Table 2. Performance data of the heat pump systems over a week. [1]
System |
Heat supply [MWh] |
Power consumption [MWh] |
COP |
Carnot COP |
Carnot efficiency [%] |
---|---|---|---|---|---|
Chillers |
70.4 |
16.7 |
4.2 | 7.7 | 55% |
Ammonia heat pumps |
105.9 |
20.1 |
5.3 | 8.1 | 65% |
Hybrid absorption/compression heat pump |
69.2 |
11.7 |
5.9 | 11.2 | 53% |
Integrated heat pump system energy consumption
Commissioned in 2018, the new dairy in Bergen, Norway replaces a former facility in Minde, Norway, which had an annual energy consumption of 0.24 kWh l−1 for the year 2015.
Using available operation data over a week in February 2020, the authors performed an energy analysis of the new dairy. Their results showed a specific energy consumption of 0.22 kWh l−1 for the investigated week, suggesting that the new integrated dairy outperformed the annual average consumption of the former facility. The energy analysis indicated that 33.0% of all energy sources in the new dairy came from either waste heat recovery or solar energy, while the system achieved a waste heat recovery rate of over 95%. Furthermore, the integrated dairy achieved external energy savings of up to 37.9%. The authors suggested that depending on the respective scenario and case, greenhouse gas emission reductions of 23.2% to 91.7% could be achieved.
Sources
[1] Ahrens, M. U., Foslie, S. S., Moen, O. M., Bantle, M., & Eikevik, T. M. (2021). Integrated high temperature heat pumps and thermal storage tanks for combined heating and cooling in the industry. Applied Thermal Engineering, 116731. https://doi.org/10.1016/j.applthermaleng.2021.116731